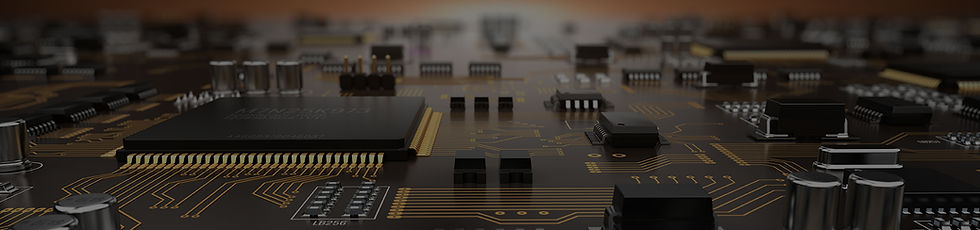
What is Rogers PCB ?
Rogers PCB refers to a type of printed circuit board that uses high-frequency laminate materials from Rogers Corporation. These materials are preferred over traditional FR-4 for applications requiring superior electrical performance.
Key Characteristics:
-
High-Frequency Performance: Rogers materials provide stable signal integrity at high frequencies, making them ideal for RF and microwave applications.
-
Low Dielectric Loss: Ensures minimal signal attenuation, essential for high-speed circuits.
-
Thermal Management: Offers superior heat dissipation and stability in high-temperature environments.
-
Mechanical Properties: Excellent dimensional stability and strength, accommodating complex PCB designs.
-
Chemical Resistance: High resistance to chemicals and moisture, enhancing durability.
Common Rogers Materials:
-
RO4000 Series: Low dielectric loss and excellent thermal stability.
-
RO3000 Series: Exceptional dimensional stability and low moisture absorption.
-
RT/duroid® Series: High-performance laminates with low dielectric constants.
Applications:
-
Telecommunications: Base stations, antennas.
-
Aerospace and Defense: Radar systems, satellite communications.
-
Automotive: Advanced driver-assistance systems (ADAS).
-
Medical Devices: Diagnostic equipment, medical imaging.
-
Industrial: Sensors, instrumentation.
In PCB prototyping, Rogers is a unique circuit board with a specific technical threshold, difficult to operate, and high cost. General PCB factories rarely fulfill orders due to the troublesome production methods and the small number of customer orders. RayMing is engaged in the PCB prototype manufacturer of Rogers high-frequency PCB boards, which can meet the various high-frequency PCB needs of customers. Currently, it can achieve 4~10 layers of ceramic pure pressure and 4~12 layers of mixed pressure.

What is Rogers Material?
Rogers Corporation is a leading global materials technology company known for its advanced circuit board laminate materials, which are integral to high-frequency, high-performance PCBs. Here's what sets Rogers materials apart:
-
Diverse Substrate Range: Rogers offers a wide array of circuit board substrate materials tailored for various applications and performance needs. Popular options include RO4000, RO3000, and RT/duroid series.
-
High-Frequency Specialization: Rogers excels in high-frequency materials for RF and microwave PCBs, ensuring precision electrical performance essential for advanced communication technologies.
-
Versatile Laminates: Both rigid and flexible circuit laminates are available, all compatible with common PCB manufacturing processes, providing flexibility in design and application.
-
Proprietary Formulations: Utilizing specialized proprietary formulations, Rogers materials boast specific dielectric, thermal, and mechanical properties, catering to the exacting needs of high-performance electronic circuits.
-
Enhanced Circuit Capabilities: Rogers' technology supports higher circuit densities, improved signal speed and integrity, and enhanced reliability, making them ideal for cutting-edge electronics.
-
Industry Compliance: Rogers materials comply with major industry standards such as UL, IPC, and RoHS. They are certified for use in aerospace, defense, telecom, automotive, and other critical sectors.
-
Global Usage: PCB manufacturers worldwide rely on Rogers materials to construct high-end circuit boards for advanced electronic devices, underlining their global footprint and industry trust.
By leveraging Rogers materials, engineers and manufacturers can achieve superior performance and reliability in their high-frequency, high-performance PCB applications.

Overview of Rogers' Circuit Board Materials
Rogers offers one of the industry’s widest selection of circuit board substrate materials to meet the needs of various applications:
RO4000 Series High Frequency Laminates
The RO4000 series consists of ceramic-filled thermoset laminates designed for exacting circuit boards operating at up to mmWave frequencies. It delivers excellent dimensional stability, low thermal expansion, and outstanding high frequency performance. Some options include:
-
RO4003TM – Most common version for wireless, aerospace, defense, and instrumentation applications.
-
RO4350BTM – Higher thermal conductivity for power circuits and heat spreading.
-
RO4450TM – Improved thermal cycle reliability performance.
-
RO4835TM – Lightweight material alternative with similar electrical features.
RO3000 Series High Frequency Laminates
The RO3000 series offers more affordable circuit materials compared to the RO4000 series, making them popular for cost-sensitive commercial applications. Options include:
-
RO3010TM – General purpose microwave material with good high frequency performance.
-
RO3006TM – Higher permittivity and thermal conductivity for power modules.
-
RO3003TM – High frequency laminate with improved insertion loss over RO3010.
RT/duroid High Frequency Laminates
RT/duroid materials are specially engineered to provide tightly controlled electrical parameters for optimal circuit functionality. They are halogen-free. Variants include:
-
RT/duroid 5870 – Low loss material for high power density in mmWave applications.
-
RT/duroid 6035HTC – High thermal conductivity and low loss for power amplifiers and antennas.
-
RT/duroid 6002 – Cost-optimized microwave laminate with improved thermal performance over RO4350B.
RO1200 Low Flow Prepregs
RO1200 low flow prepregs consist of liquid crystal polymer films designed primarily for multilayer PCB constructions requiring excellent dimensional stability. Common versions are RO1200TM and RO1220TM.
TMM Thermoset Microwave Materials
The TMM series offers a selection of thermoset micro-dispersed ceramic-filled materials covering a wide range of dielectric constants for broadband applications. Options include TMM3, TMM4, TMM6, TMM10i, and more.
lexible LCP and PTFE Films
Rogers’ flexible circuit materials provide excellent high frequency performance in a thin, lightweight form factor. These include ULTRALAM® liquid crystal polymer (LCP) films and RT/duroid® PTFE composites.
Other Specialty Materials
Additional Rogers’ materials technologies include ceramic-filled thermal endmatch materials, damping materials, beam window materials, polyimide films, and more for specific applications.
Rogers also offers quick-turn prototyping materials under its ProtoBONDTM brand.
Benefits of Rogers Materials for PCBs

Using Rogers materials for circuit board fabrication provides these key advantages:
High Frequency Performance – Provides stable dielectric constant and low loss characteristics for optimal electrical functionality in RF, microwave, and millimeter wave applications. Allows higher operating frequencies.
Thermal Management – Specialized formulations available with high thermal conductivity, low coefficient of thermal expansion, and excellent thermal stability for managing heat in circuit boards. Critical for power devices.
Miniaturization – Consistent and reliable electrical properties allow construction of higher complexity boards, components, circuits, and electrical features within a given area for greater miniaturization.
Signal Integrity – Excellent dimensional stability along with fine microstructures result in smooth copper surfaces that greatly improve signal speed, quality, and signal integrity through PCB traces.
Reliability – Long-term material stability, adhesion, and durability support reliability requirements of defense, aerospace, automotive, and other long-life applications.
Design Flexibility – Wide range of material thicknesses, sizes, certifications, dielectric constants, loss tangents, and other parameters provides extensive design flexibility.
Ease of Processing – Compatible with standard circuit board fabrication techniques like imaging, drilling, plating, and assembly allowing use with existing PCB processes and equipment.
Regulatory Compliance – Materials comply with major environmental and regulatory standards for use in stringently controlled industries and applications.
Rogers PCB and Laminate Manufacturing Process
Material Acquisition and Quality Assurance: Rogers collaborates with global distributors to supply various PCB materials in sheet, panel, or roll formats. Stringent quality checks ensure adherence to dimensional tolerances and material specifications upon receipt.
Panel Preparation and Precision Tooling: Rogers laminates are precisely cut into panels and drilled with tooling holes for precise alignment during subsequent processes.
Imaging and Etching: Surfaces of Rogers laminates are coated with photoresist and exposed to define circuit patterns. Etching processes selectively remove exposed copper to form circuit traces.
Automated Optical Inspection and Plating: Automated optical inspection verifies trace accuracy and quality before surfaces undergo copper plating. Additional coatings, like solder masks and finishes, are applied where necessary.
Layer Lamination and Microvia Drilling: Rogers boards undergo lamination under controlled heat and pressure to form multilayer structures. Microvia drilling ensures precise interconnections between layers.
Routing, Testing, and Quality Assurance: Post lamination, boards are routed to final dimensions. Rigorous electrical testing verifies circuit continuity and performance against specified parameters. Comprehensive quality assurance protocols identify and rectify any defects.
Final Finishing and Packaging: Optional protective coatings safeguard PCBs from environmental elements. After thorough cleaning and baking, boards are meticulously packaged for safe transport to end-use manufacturers.
Through optimized manufacturing processes tailored to Rogers materials, PCB fabricators achieve superior quality and reliability, meeting the demands of high-performance applications in industries such as aerospace, telecommunications, and automotive electronics.
Flexible PCB Design Considerations
Designing a reliable flexible PCB requires addressing the dynamic bending aspects with specialized guidelines:
Trace Width and Spacing: Wider spacing for narrower traces in dynamic regions is essential to avoid cracks. A 2:1 ratio of spacing to trace width is recommended.
Bend Radius: Route traces perpendicular to bend axes. Maintain at least a 3X base thickness for static bends and 10X for dynamic bends.
Coverlay Voids: Minimize voids where traces are exposed to prevent wear, especially in dynamic bend zones.
Reinforcement: Use stiffeners in multilayer regions to prevent buckling and wrinkling during bending.
Adhesives: Employ high-performance flexible adhesives like acrylic for durability in dynamic flex applications.
Vias: Use tear-drop shaped vias with adequate annular rings to prevent crack propagation from drill hole edges.
Corners: Round sharp trace corners with higher radii to reduce stress concentrations. Avoid angled traces at corners.
Pads: Utilize rounded rectangle or circular pads and thermally relieve pads in flexing areas with neckdowns.
By following these guidelines, flex PCBs can be designed to withstand millions of flexing cycles, ensuring long product lifetimes and reliability in various applications.
Major Applications of Rogers Materialsions
The high frequency capabilities and reliable performance of Rogers materials makes them well suited for:
-
Wireless Communications – Used in 5G NR mmWave antennas, massive MIMO arrays, remote radio heads, base stations, backhaul links, and other wireless infrastructure.
-
Satcom & Radar – Used in satellite communications, phased array radar systems, GPS equipment, and other high frequency aerospace and defense electronics.
-
Automotive Radar – Used in collision avoidance radar PCBs for advanced driver assistance systems in modern vehicles.
-
High-Speed Data – Used in networking equipment, data centers, test equipment, and oscilloscopes for high-bandwidth applications.
-
Smart Weaponry – Used in “smart” munitions, guided missiles, drones, and other military electronics requiring reliable high frequency circuit boards.
-
Aerospace & Avionics – Used in in-flight entertainment systems, communications, onboard electronics, and other commercial and military aircraft systems.
-
5G Phased Arrays – Used in high performance 5G beamforming antenna arrays for improved speed and coverage.
-
Medical Imaging – Used in MRI, X-Ray, and other imaging equipment operating at UHF, microwave, and mmWave frequencies.
-
Test & Measurement – Used in oscilloscopes, signal generators, and other lab equipment for high-frequency measurements.
-
Radar Housings – Used in structural radomes, modules, and housings for protecting sensitive radar electronics.
-
Industrial/Scientific – Used in high power industrial RF generators and processing equipment used for scientific research.
The specialized high frequency properties of Rogers materials makes them a top choice for these cutting-edge applications.
Designing Rogers PCBs
To effectively utilize Rogers materials in circuit board designs, engineers should adhere to these optimized guidelines:
Material Selection: Choose the appropriate Rogers laminate based on requirements such as dielectric constant, loss tangent, thermal conductivity, and mechanical properties to ensure optimal performance.
Utilize Rogers’ Models: Employ Rogers’ material models for simulations to accurately predict and optimize circuit performance, especially in high frequency applications.
Follow Layout Guidelines: Design layouts should conform to manufacturing capabilities and constraints, including:
-
Trace width and spacing
-
Minimum hole size
-
Impedance tolerances
-
Line-to-line spacing
-
Layer stackup configuration
-
Design for Thermal Management: Implement effective thermal management strategies to dissipate heat from components, preventing performance degradation and ensuring reliability over time.
Consider Coefficients: Account for material-specific coefficients such as thermal expansion coefficient to mitigate potential issues related to dimensional stability and reliability.
Leverage Technical Support: Take advantage of Rogers’ comprehensive technical support, resources, and expertise in high frequency design techniques to optimize board performance and reliability.
By adhering to these guidelines, engineers can harness the full potential of Rogers circuit board materials, tailored precisely to meet the specific needs and challenges of their applications.
