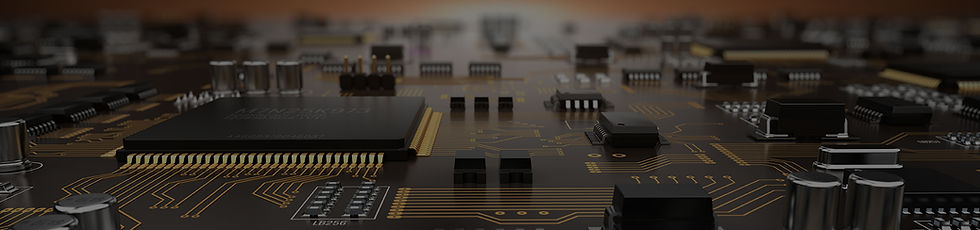
O que é um conjunto de construção de caixa em eletrônica de PCB?
Os serviços de integração de sistemas SUNSOAR fornecem soluções de montagem Box Build abrangentes, incluindo Montagem de Produto, Montagem de Cabos, Montagem em Nível de Sistema e vários recursos de teste para implantação eficaz. Atualmente, atendemos a pedidos de menos de 10.000 unidades.
Introdução
A montagem de construção de caixa é o estágio final da fabricação de eletrônicos, abrangendo a montagem de placas de circuito impresso (PCBs), cabos e vários componentes eletrônicos dentro de um chassi ou invólucro totalmente fechado. Este processo combina considerações mecânicas, elétricas e estéticas para produzir um produto eletrônico acabado pronto para implantação pelo usuário final.
Executar a montagem de construção de caixa exige experiência em gerenciamento de projetos, coordenação meticulosa da cadeia de suprimentos, práticas rigorosas de controle de qualidade, técnicas de integração mecânica adequadas e protocolos de teste abrangentes. As empresas especializadas em construção de caixa são normalmente chamadas de fabricantes contratados ou provedores de serviços de fabricação eletrônica (EMS).
-
Montagem de construção de caixa
-
Montagem de protótipo
-
PCB multicamadas
-
Teste de PCBA
O que é Box Build Assembly
Visão geral do processo de montagem de caixa
A montagem de caixa abrange vários estágios críticos:
Kitting: Reunir todos os materiais necessários, incluindo PCBs, cabos, gabinetes, fixadores e acessórios.
Submontagem: Integrar módulos menores, como fontes de alimentação, drives e chicotes de fios.
Montagem de PCB: Montar PCBs e componentes eletrônicos no gabinete usando espaçadores, parafusos ou adesivos. Interconectar componentes com cabos.
Integração: Adicionar elementos suplementares, como suportes, alças e interfaces de controle ao gabinete.
Teste: Realizar testes rigorosos de garantia de qualidade para garantir funcionalidade, segurança e conformidade com os padrões regulatórios.
Embalagem: Finalizar o produto com manuais do usuário, embalagem e etiquetagem.
A complexidade da montagem de caixa varia com base em fatores como diversidade de componentes, complexidade do gabinete e volume de produção.
Benefícios da montagem de caixa
A utilização de serviços de montagem de caixa oferece várias vantagens:
Tempo de colocação no mercado acelerado: Fabricantes contratados especializados agilizam os processos de desenvolvimento e lançamento de produtos.
Foco nas competências essenciais: as marcas podem se concentrar em inovação e design enquanto terceirizam tarefas de fabricação.
Eficiência de custos: os provedores de EMS alavancam economias de escala em aquisição e produção, levando a economias de custos.
Garantia de qualidade: os provedores de EMS estabelecidos mantêm medidas rigorosas de controle de qualidade e protocolos de teste abrangentes.
Flexibilidade e escalabilidade: os volumes de produção podem ser ajustados rapidamente para atender às flutuações da demanda do mercado.
Serviço abrangente: os provedores de EMS oferecem soluções de ponta a ponta, incluindo serviços de sourcing, montagem, teste, logística e suporte.

Indústrias que usam a fabricação de caixas
Algumas indústrias comuns que dependem de serviços de montagem de caixas:
Eletrônicos de consumo – Consoles de jogos, home theaters, alto-falantes inteligentes
Equipamentos industriais – Fontes de alimentação, acionamentos de motor, controles de automação, instrumentos de teste
Telecomunicações/redes – Roteadores, switches, servidores, estações base
Dispositivos médicos – Sistemas de imagem, analisadores, monitores
Automotivo – Sistemas de navegação, estações de carregamento de veículos elétricos, infoentretenimento automotivo
Quiosques e máquinas de venda automática – Autoatendimento, quiosques de venda de ingressos, máquinas de venda automática
Defesa e aeroespacial – Eletrônicos reforçados, caixas de aviônicos
Processo de montagem do Box Build explicado
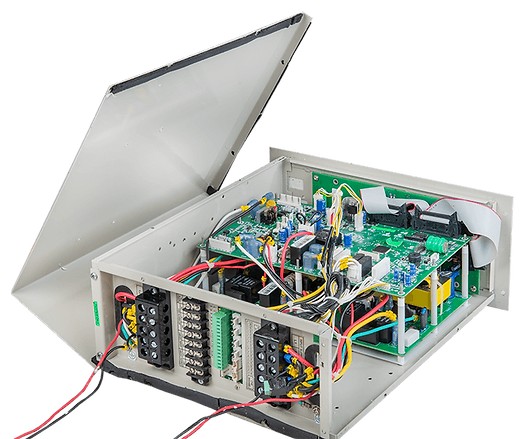
Kitting, também conhecido como planejamento de materiais, inicia o processo de montagem da caixa, garantindo que todos os componentes e peças necessários sejam adquiridos antes da produção.
Os componentes incluem:
1. Placas de circuito impresso (obtidas de fornecedores de PCB ou produzidas internamente por meio de linhas SMT)
2. Cabos, fios e conectores
3. Gabinetes, suportes e alças
4. Fixadores como parafusos, rebites e espaçadores
5. Acessórios como sensores, antenas e teclados
6. Etiquetas, materiais de embalagem e documentação
7. Ferramentas de montagem e teste
Kitting eficiente evita atrasos na produção devido a peças faltantes e minimiza os custos de manutenção de estoque. Os componentes podem ser obtidos globalmente de vários fornecedores, ressaltando a importância de uma logística robusta e do gerenciamento da cadeia de suprimentos.
Melhores práticas para kitting eficiente:
1. Classificação de peças: categorize as peças em grupos (A, B, C) com base na frequência de uso, priorizando peças do Grupo A de alta demanda.
2. Níveis mínimo-máx.: estabeleça limites mínimos e máximos de estoque para cada categoria de peças para otimizar os níveis de estoque.
3. Planejamento de demanda: utilize dados históricos e previsões de vendas para antecipar requisitos futuros de componentes.
4. Rastreamento de tempo de entrega: considere os prazos de entrega para componentes de vários fornecedores para evitar atrasos.
5. Indicadores visuais: implemente sistemas Kanban e codificação de cores para monitorar o consumo de peças e as necessidades de reposição.
6. Código de barras: use etiquetas com código de barras para identificação e rastreamento precisos de peças em todos os processos de montagem.
7. Ferramentas de software: empregue sistemas MRP (Material Requirements Planning) e ERP (Enterprise Resource Planning) para planejamento automatizado de materiais e gerenciamento de estoque.
O gerenciamento eficaz da cadeia de suprimentos é crucial para operações de montagem de caixas sem problemas. As principais práticas incluem:
1. Seleção de fornecedores: Avalie os fornecedores com base em qualificações e capacidades. Obtenha certificados de conformidade e avalie sua capacidade de atender aos requisitos de qualidade e entrega.
2. Fornecimento duplo: Mitigue os riscos associados a componentes críticos identificando e qualificando fornecedores alternativos.
3. Planejamento de estoque: Utilize previsões de demanda e análise de prazo de entrega para otimizar os níveis de estoque. Implemente estratégias para equilibrar a disponibilidade de estoque com os requisitos de capital de giro.
4. Ordens de compra: Garanta a emissão oportuna de ordens de compra aos fornecedores. Acelere os pedidos conforme necessário para manter os cronogramas de produção.
5. Preparação do fornecedor: Sempre que possível, localize os fornecedores perto das instalações de produção para agilizar a logística e reduzir os prazos de entrega.
6. Otimização logística: Otimize as rotas de remessa e os modos de transporte para minimizar os custos e maximizar a eficiência. Consolide as remessas para obter economias de escala.
Uma estratégia de cadeia de suprimentos resiliente atenua o risco de escassez de componentes que podem interromper os cronogramas de produção. Práticas eficazes de gerenciamento de estoque aumentam ainda mais a eficiência operacional e a estabilidade financeira.
Submontagem
Em montagens complexas de caixas, a submontagem precede a integração final, simplificando o processo ao criar módulos menores e gerenciáveis. Os tipos comuns de submontagens incluem:
1. Fontes de alimentação: conversores CA-CC e CC-CC montados separadamente devido ao volume do componente.
2. Compartimentos de unidade: alojamento para discos rígidos e unidades de estado sólido.
3. Painéis de E/S: integração de portas, botões e módulos de exibição em painéis acessíveis.
4. Chicotes de fios: cabos pré-montados adaptados a comprimentos específicos e requisitos de conectores.
As submontagens aumentam a eficiência e a qualidade ao permitir testes independentes para detectar defeitos precoces. As submontagens reutilizáveis de várias execuções de produção garantem a consistência. A granularidade ideal das submontagens equilibra a complexidade e a eficiência.
Montagem de PCB
1. Esta fase envolve a montagem de PCBs e componentes eletrônicos em gabinetes de metal ou plástico. As considerações incluem:
2. Montagem: Utilizar furos pré-rosqueados, pilares ou espaçadores para fixação de PCB.
3. Design térmico: Garantir dissipação de calor adequada e folga dentro do gabinete.
4. Planejamento de layout: Facilitar a montagem com folga suficiente para componentes e posicionamento estratégico do conector.
Cabeamento e fiação
1. PCBs internos são interconectados usando fios, cabos e conectores. As melhores práticas incluem:
2. Roteamento: Empregar dutos de fiação, eletrodutos e alívios de tensão para gerenciamento seguro de fios.
3. Minimização do comprimento: Encurtar o comprimento dos fios para otimizar o roteamento e evitar superaquecimento.
4. Etiquetagem: Marcar claramente as extremidades dos cabos para evitar fiação incorreta, usando conectores exclusivos para identificação.
Integração
1. Integrar componentes adicionais ao gabinete:
2. Elementos da interface do usuário: Botões, interruptores, teclados, visores.
3. Componentes mecânicos: Suportes, alças, saídas de ar, filtros.
4. Marca: Logotipos, decalques, marcações regulatórias.
O alinhamento e o ajuste adequados garantem coerência funcional e estética, refletindo o design industrial e a identidade da marca.
Testes e controle de qualidade
1. Após a montagem mecânica, testes rigorosos garantem a confiabilidade do produto:
2. Testes de funcionalidade: Verificação da segurança elétrica, funcionalidade operacional e durabilidade ambiental.
3. Segurança e conformidade: Adesão aos padrões de segurança (UL, CE), compatibilidade eletromagnética (EMC/EMI) e regulamentações ambientais (RoHS).

Testes específicos do produto
1. Inspeção visual: garante ajuste, acabamento, precisão de etiquetagem e aparência cosmética geral.
2. Calibrações: ajusta eletrônicos de medição, como geradores de sinal, para operação precisa.
3. Teste de burn-in: submete produtos a operação prolongada com energia para simular tensões ambientais.
4. Teste de vibração, queda e choque: conduzido com base nos requisitos de aplicação do produto.
5. Teste acústico: mede os níveis de som e o ruído do ventilador de resfriamento para verificar o desempenho acústico.
6. Teste térmico: monitora a distribuição de temperatura em gabinetes usando sondas térmicas.
Auditoria funcional final
1. Teste funcional de 100%: garante que todas as unidades que saem da produção atendam às especificações operacionais.
2. Critérios de teste: está em conformidade com os requisitos e especificações detalhadas do produto.
3. Detecção e correção de falhas: identifica e resolve problemas para garantir a confiabilidade do produto.
Testes abrangentes garantem que cada conjunto de construção de caixa atenda a rigorosos padrões de qualidade, segurança e confiabilidade. As correções são feitas proativamente para entregar produtos impecáveis aos clientes.
Embalagem e logística
As etapas finais incluem:
1. Fixação de tampas ou painéis superiores e inferiores para envolver totalmente o chassi.
2. Aplicação de películas plásticas protetoras sobre áreas vulneráveis.
3. Adição de acessórios como cabos de alimentação, cabos, suportes, CDs.
4. Inserção de manuais do usuário, cartões de garantia, folhetos de registro.
5. Afixação de etiquetas com números de peça, números de série, logotipos, avisos e certificações.
antiestático
1. Plástico-bolha, espuma, almofadas de ar para proteger os produtos acabados.
2. Embalar cada unidade em uma caixa individual com amortecimento adequado.
3. Paletizar caixas e envoltório retrátil para remessa.
4. Coordenar a logística com o depósito ou centros de distribuição do cliente.
A embalagem cuidadosa previne danos e melhora a experiência de desembalagem do cliente. As unidades são enviadas por via rodoviária, aérea ou marítima, conforme o prazo de entrega e a localização geográfica.
Vantagens de usar serviços de montagem Box Build
Tempo de colocação no mercado mais rápido
A terceirização de construções de caixas para um fabricante contratado acelera drasticamente os lançamentos de produtos e o tempo de colocação no mercado.
A configuração de uma linha de produção e instalação inteiras internamente pode levar anos e um investimento significativo em ferramentas e equipamentos. Um fornecedor especializado de EMS, no entanto, já estabeleceu linhas de montagem, cadeias de suprimentos, capacidades de teste e recursos prontos para uso.
Ao confiar projetos mecânicos e elétricos detalhados ao fornecedor de EMS, a equipe de engenharia de produtos pode acelerar o ciclo de desenvolvimento, trazendo produtos inovadores ao mercado mais rapidamente.
Principais aceleradores do tempo de colocação no mercado:
1. Prontidão instantânea da produção: inicie a produção imediatamente usando linhas de montagem existentes.
2. Eficiência comprovada: aproveite os processos de fabricação e sistemas de qualidade estabelecidos.
3. Cadeia de suprimentos simplificada: acesse uma rede de fornecedores confiáveis para fornecimento eficiente de peças.
4. Escalabilidade flexível: ajuste rapidamente os volumes de produção para atender às flutuações da demanda.
5. Prototipagem rápida: itere designs rapidamente para otimizar os recursos e o desempenho do produto.
Foco nas principais competências
Marcas e OEMs podem concentrar recursos internos em competências críticas, como design de produto, desenvolvimento de software e engajamento do cliente. Delegar operações de fabricação permite foco dedicado em inovação e diferenciação de mercado.
Fabricantes contratados trazem habilidades especializadas, melhores práticas e padrões de qualidade rigorosos para a fabricação de eletrônicos. Essa abordagem estratégica de terceirização poupa OEMs de investimentos pesados em infraestrutura de produção e desenvolvimento de expertise.
Áreas para foco interno aprimorado:
1. Design inovador: pioneirismo na estética do produto e na experiência do usuário.
2. Engenharia de ponta: avanço de capacidades tecnológicas e propriedade intelectual.
3. Diferenciação de software: criação de soluções e aplicativos de software específicos de domínio.
4. Construção de marca: elevação da presença no mercado e fidelidade do cliente por meio de iniciativas estratégicas.
Eficiência de Custo
1. A parceria com um fornecedor de EMS estabelecido leva a economias de custo significativas em comparação à produção interna.
2. Operação sem capital: Evite despesas iniciais em equipamentos com custos flexíveis de montagem por unidade.
3. Economias de escala: Beneficie-se de descontos por volume em componentes por meio da agregação coletiva de pedidos.
4. Gestão de estoque enxuta: Minimize os níveis de estoque com processos just-in-time (JIT), reduzindo o capital retido no estoque.
5. Logística otimizada: Reduza as despesas de envio com gerenciamento de logística centralizado.
Vantagem competitiva
Relatórios sugerem que a parceria com fornecedores de EMS pode reduzir os custos de fabricação em até 30%, aumentando a competitividade e a lucratividade.

Qualidade e confiabilidade
A fabricação de eletrônicos exige consistência na qualidade da soldagem, seleção de peças, métodos de teste, controle de ESD e mão de obra. Os provedores de EMS especializados têm experiência institucional e conhecimento em controle de qualidade que é difícil igualar com a produção interna.
A terceirização de construções de caixas melhora a confiabilidade do produto por meio de:
1. Instalações de produção certificadas – ISO, IATF 16949, fluxos de trabalho 5S.
2. Processos automatizados – À prova de erros, pontos de inspeção, visão de máquina.
3. Ferramentas mais recentes – Equipamentos de alta precisão, como soldagem seletiva.
4. Técnicos qualificados – Engenheiros de soldagem, montagem e teste certificados pelo IPC.
5. Controle de componentes – Listas de fornecedores aprovados, prevenção de peças falsificadas.
6. Repetibilidade – Processos padronizados em todos os produtos.
7. Teste de confiabilidade – Teste HALT, burn-in e triagem de estresse ambiental.
O resultado final são produtos confiáveis com menores custos de reparo em garantia.
Flexibilidade e Escalabilidade
Os provedores de EMS oferecem tanto prototipagem de baixo volume quanto produção em massa de alto volume. Os clientes podem começar com produção inicial de baixa taxa (LRIP) e aumentar rapidamente conforme a demanda. Surtos repentinos de demanda ou escassez podem ser controlados ajustando rapidamente a capacidade.
Essa flexibilidade vem de:
1. Linhas de montagem modulares – Adicione/remova módulos de equipamento rapidamente.
2. Linhas de vários produtos – Programe a produção em instalações compartilhadas.
3. Trocas rápidas – Alterne entre variantes de produtos com eficiência.
4. Trabalhadores temporários – Atenda à demanda máxima usando uma força de trabalho flexível.
5. Sourcing JIT – Otimize e ajuste pedidos com fornecedores com frequência.
A escalabilidade e agilidade minimizam os riscos de flutuações de demanda. As introduções de novos produtos também se beneficiam dos recursos de ramp up/ramp down.
Serviços One-Stop-Shop
O parceiro EMS fornece um conjunto holístico de serviços além de apenas montagem e encaixotamento de PCB:
1. Design de produto – Design para entradas de manufaturabilidade (DFM). Revisões de layout de PCB. Modelagem 3D.
2. Prototipagem – Prototipagem funcional de novas inovações de produtos.
3. Teste – Teste de estresse ambiental. Teste de conformidade. Análise de falhas de campo.
4. Cadeia de suprimentos – Componentes de sourcing. Estoque gerenciado pelo fornecedor (VMI).
5. Engenharia de sustentação – Manutenção do produto. Monitoramento de obsolescência. Reprojetos.
6. Reparos e garantia – Gerenciamento de devoluções e reparos.
7. Distribuição – Armazenagem. Atendimento de pedidos. Envio.
Os clientes se beneficiam do suporte centralizado do berço ao túmulo, do design industrial ao gerenciamento do fim da vida útil sob o mesmo teto. A coordenação simplificada também garante melhor consistência em todo o ciclo de vida do produto.
Principais considerações para o sucesso do projeto Box Build
Colaboração Inicial
A colaboração efetiva entre o OEM e o parceiro EMS no início é crucial para mitigar problemas posteriores. Concentre-se em finalizar especificações críticas antecipadamente:
1. Design Industrial: Defina materiais de gabinete, estética e marca.
2. Seleção de Componentes: Revise a Lista de Materiais (BOM) para prazos de entrega, considerações de custo e potencial obsolescência.
3. Otimização da BOM: Identifique peças de substituição para custo-efetividade e disponibilidade.
4. Design para Fabricação (DFM): Conduza análises para otimizar a eficiência de montagem e teste.
5. Processos de Fabricação: Estabeleça planos de qualidade e estratégias de teste.
6. Padrões de Conformidade: Garanta o alinhamento com os requisitos de segurança, EMC/EMI e regulatórios.
7. Cronograma do Projeto: Defina cronogramas e marcos de produção.
A colaboração antecipada e a construção conjunta de protótipos evitam atrasos, garantindo que os requisitos sejam atendidos. Revisões regulares de design e verificações de progresso mantêm o ritmo do projeto.
Planejamento de controle de qualidade
Desenvolva um plano de qualidade robusto abrangendo:
1. Pontos de inspeção: implemente verificações de qualidade em processo em estágios críticos.
2. Métodos de teste: inclua testes funcionais, ambientais, de confiabilidade e segurança.
3. Rastreabilidade: mantenha a serialização das peças, códigos de data e documentação abrangente.
4. Protocolos ESD: aplique medidas de controle de descarga eletrostática (por exemplo, pulseiras, tapetes).
5. Critérios de aceitação: estabeleça métricas claras de aprovação/reprovação para inspeções e testes.
6. Documentação: utilize formulários e listas de verificação padronizados para clareza operacional.
7. Treinamento: forneça treinamento rigoroso sobre protocolos de teste e inspeção.
8. Melhoria contínua: conduza análises de capacidade do processo, defina limites de controle e implemente ações corretivas.
A atenção rigorosa ao controle de qualidade desde o início minimiza os defeitos e garante a confiabilidade do produto.
Desenvolvimento do Processo de Fabricação
Prepare os processos de montagem e teste para prontidão de produção durante a prototipagem:
1. Otimização do Fluxo de Trabalho: Simplifique as etapas de montagem para eficiência ergonômica.
2. Viabilidade da Automação: Avalie as opções para processos automatizados, como parafusamento.
3. Otimização do Teste: Depure e valide rotinas de teste para precisão e confiabilidade.
4. Validação do Processo: Conduza estudos de capacidade e estabeleça limites de controle.
5. Instruções do Operador: Desenvolva instruções de trabalho visuais e guias para clareza.
6. Treinamento: Treine o pessoal e audite regularmente a adesão ao processo.
7. Projeto de Fixação: Garanta que as fixações de montagem e teste espelhem as configurações do produto final.
O desenvolvimento abrangente do processo elimina ineficiências, abrindo caminho para um aumento contínuo da produção.
Gestão da Cadeia de Suprimentos
Garanta o gerenciamento proativo de compras e fornecedores para otimizar a eficiência da produção:
1. Seleção do Fornecedor: Avalie as qualificações e capacidades do fornecedor e obtenha certificados de conformidade.
2. Sourcing duplo: mitigue o risco identificando fornecedores alternativos para componentes críticos.
3. Planejamento de estoque: planeje estrategicamente os níveis de estoque com base nas previsões de demanda e nos prazos de entrega.
4. Ordens de compra: colocação oportuna e processamento rápido de pedidos de peças, conforme necessário.
5. Preparação do fornecedor: otimize a logística localizando fornecedores perto das instalações de produção, quando possível.
6. Otimização logística: consolide remessas e otimize rotas para entrega eficiente de peças.
Uma estratégia robusta de cadeia de suprimentos evita atrasos devido à escassez de peças e minimiza os requisitos de capital de giro por meio do gerenciamento eficaz de estoque.