What is the difference between wave soldering and reflow soldering?
- afax TE.
- Aug 14, 2024
- 2 min read
Wave soldering and reflow soldering are two key methods used in the assembly of printed circuit boards (PCBs), but they are suited to different types of components and assembly requirements. Here’s a breakdown of the key differences:
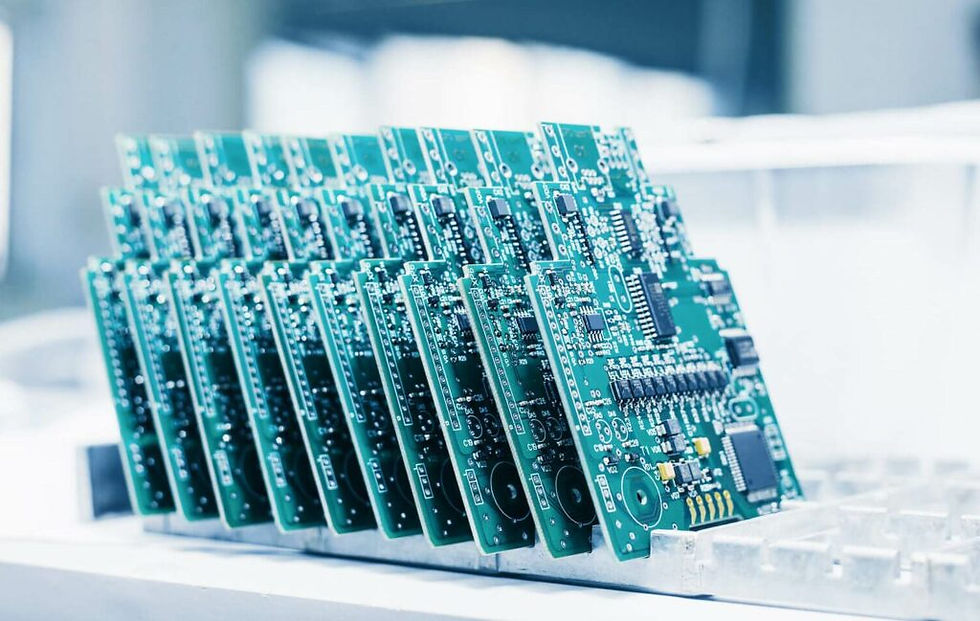
1. Process Type:
Wave Soldering:
Primarily used for through-hole components.
In this process, the PCB is passed over a wave of molten solder. The solder adheres to the exposed metallic areas on the PCB, creating electrical connections between the component leads and the PCB pads.
Reflow Soldering:
Mainly used for surface-mount technology (SMT) components.
In reflow soldering, solder paste (a mixture of solder powder and flux) is applied to the PCB pads. The PCB, with components placed on it, is then heated in an oven where the solder paste melts and solidifies, creating the electrical connections.
2. Components Supported:
Wave Soldering:
Best for through-hole components and some mixed technology boards (where both through-hole and SMT components are present).
Less suitable for fine-pitch SMT components.
Reflow Soldering:
Ideal for SMT components, including fine-pitch and small-sized components like chips and resistors.
Can also accommodate some through-hole components using special soldering techniques (e.g., pin-in-paste).
3. Equipment and Complexity:
Wave Soldering:
Simpler in terms of equipment design but requires careful control of solder temperature and wave parameters.
The process can be less precise compared to reflow, especially with complex boards.
Reflow Soldering:
Requires more complex and expensive equipment (reflow oven) and precise control of temperature profiles.
More versatile and capable of handling more intricate and densely populated PCB designs.
4. Application Scenarios:
Wave Soldering:
Commonly used in the production of through-hole components and in older or simpler electronic assemblies.
Also used in mass production where through-hole components are predominant.
Reflow Soldering:
Predominantly used in modern electronics manufacturing where SMT dominates.
Preferred for complex and high-density PCB assemblies like smartphones, computers, and other consumer electronics.
5. Soldering Quality and Challenges:
Wave Soldering:
Can result in solder bridges and other defects if not carefully controlled.
May require additional steps for SMT components if they are present on the same board.
Reflow Soldering:
Typically provides higher precision and reliability, especially with advanced SMT designs.
The process must be carefully managed to prevent issues like solder balls, tombstoning, or cold joints.
#PCBA #WaveSoldering #ReflowSoldering #PCBAssembly #SurfaceMountTechnology #ThroughHoleTechnology #ElectronicsManufacturing
Conclusion:
Wave soldering is most suitable for simpler, through-hole assemblies, whereas reflow soldering is essential for modern, high-density SMT boards. Understanding the differences between these two processes helps manufacturers choose the right method for their specific assembly needs.
Comments