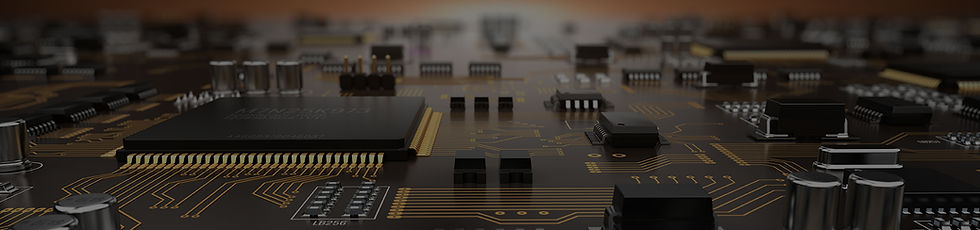
Ensuring the reliability and quality of Printed Circuit Boards (PCBs) and Printed Circuit Board Assemblies (PCBAs) is paramount. Testing these components rigorously is essential to meet the high standards required for modern electronic devices.
1. Bare PCB Testing
Objective: Ensure that the PCB, before assembly, is free of defects such as shorts, opens, and incorrect copper thickness.
Techniques:
Electrical Testing (ET): Utilizes test fixtures and flying probes to check for continuity and insulation resistance. It identifies shorts and open circuits.
Automated Optical Inspection (AOI): Uses high-resolution cameras to detect surface defects like scratches, solder mask issues, and misalignments.
Bed-of-Nails Testing: Employs a fixture with numerous pins that contact the PCB pads, testing multiple points simultaneously for continuity and functionality.
2. Assembly Level Testing (PCBA Testing)
Objective: Verify that the assembled PCB functions as intended and meets design specifications.
Techniques:
In-Circuit Testing (ICT): Tests individual components on the board to ensure they are correctly placed and functioning. ICT can measure resistance, capacitance, and signal integrity.
Functional Testing: Simulates the operational environment of the PCB, applying real-world signals and loads to verify the functionality of the complete assembly. This test checks for correct operation under normal and extreme conditions.
Burn-In Testing: Subjects the PCBAs to elevated temperatures and loads over extended periods. This stress test identifies early failures and ensures long-term reliability.
3. Specialized Testing
Objective: Address specific requirements based on the end-use application of the PCB/PCBA.
Techniques:
Environmental Stress Testing (ESS): Includes thermal cycling, humidity testing, and vibration testing to assess the assembly's durability under harsh conditions.
Signal Integrity Testing: Critical for high-frequency and high-speed applications. Ensures signal transmission without distortion or loss.
X-ray Inspection: Used for inspecting hidden solder joints, such as those in Ball Grid Arrays (BGAs) and other components with inaccessible connections.
Boundary Scan Testing: Uses a standardized method (IEEE 1149.1) to test interconnections and internal logic of components without physical test points.
4. Quality Assurance (QA) Procedures
Objective: Maintain consistent quality and reliability across all manufacturing batches.
Techniques:
Statistical Process Control (SPC): Monitors production processes through statistical methods to detect and control variability.
Total Quality Management (TQM): Involves continuous improvement processes and practices to enhance product quality and customer satisfaction.
Failure Analysis: When defects are identified, thorough root cause analysis is performed to understand and rectify the issue, preventing recurrence.
5. Documentation and Standards Compliance
Objective: Ensure traceability and adherence to industry standards.
Techniques:
Comprehensive Documentation: Maintain detailed records of all test procedures, results, and corrective actions. This ensures traceability and accountability.
Compliance with Standards: Adhere to industry standards such as IPC-A-600 for PCB fabrication and IPC-A-610 for electronic assembly. These standards define the acceptability criteria for various aspects of PCB and PCBA quality.
Conclusion:
PCB and PCBA testing is a multifaceted process critical to ensuring the performance, reliability, and longevity of electronic products. By employing a combination of advanced testing techniques, adhering to rigorous quality assurance procedures, and maintaining compliance with industry standards, manufacturers can deliver products that meet the high expectations of today’s technology-driven market.
At SUNSOAR, we are committed to upholding these standards through our comprehensive testing protocols, ensuring that every product we deliver stands up to the highest levels of scrutiny and performance. Our dedication to quality and customer satisfaction is unwavering, making us a trusted partner in the electronics manufacturing industry.
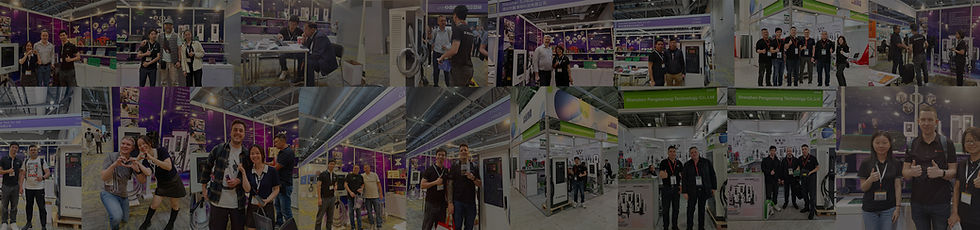