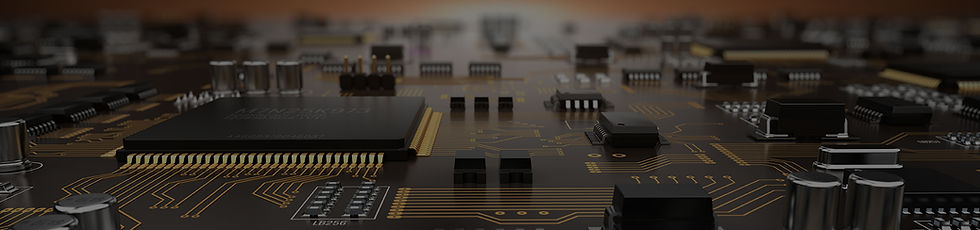
はじめに
多層プリント基板 (PCB) は、FR-4 などの誘電体で分離された 2 層以上の導電性銅層で構成されています。これらの PCB は、両面および内部埋め込み層に配置できるため、コンポーネント密度が向上し、複雑なデジタル回路、RF/マイクロ波システム、高速コンピューティング、および高度な相互接続性を必要とするその他のアプリケーションに最適です。
この記事では、多層 PCB テクノロジの詳細な概要を説明します。内容は次のとおりです。
1. 多層 PCB の製造プロセス
2. 材料と構造
3. 設計上の重要な考慮事項
4. モデリングと分析
5. 熱管理
6. 信号の整合性
7. コストのトレードオフ
信頼性要因
多層 PCB の機能と設計のベスト プラクティスを理解することは、電子製品開発でその利点を活用するために不可欠です。
-
多層 PCB とは: 製造、設計、コストとは?
-
6 層 PCB
-
8 層 PCB
-
10 層 PCB
-
12 層 PCB
多層PCB製造プロセス
多層 PCB の製造には、複数の両面回路層を 1 つの統合基板に結合するための特殊な連続積層プロセスが必要です。一般的な製造手順は次のとおりです。
1. 内層の形成
処理済みの銅張りラミネート上に回路トレースを定義するためのフォトリソグラフィー パターン化。
レイヤー レジストレーション ターゲットとツール ホールの追加。
トレースの電気テストの実施。
ラミネーション用の表面準備。
2. レイヤー ラミネーション
シート ラミネーション プレスを使用してレイヤーを結合します。
コア、プリプレグ、銅、誘電体のスタックアップを配置します。
温度と圧力で硬化させてラミネートを形成します。
3. ドリル穴あけ
ツールとビア ホールを作成するための高精度のドリル。
正確なレジストレーションを確保して、各レイヤーを正確にドリルします。
4. ホール メッキ
薄い導電層としての無電解銅メッキ。
電解銅めっきにより、必要な厚さを実現します。
銅は内層とドリル穴に堆積します。
5. 外層処理
液体フォトイメージング (LPI) ソルダーマスクを適用します。
識別マーク付きの凡例を印刷します。
外層回路のパターン化とエッチング。
個々の PCB へのパネル配線。
6. テストと品質保証
自動光学検査 (AOI)。
ネット接続テスト。
インピーダンス、高電圧、および機能テスト。
寸法品質管理。
これらの手順により、幅広い高度な電子アプリケーションに適した高品質で信頼性の高い多層 PCB が確実に製造されます。
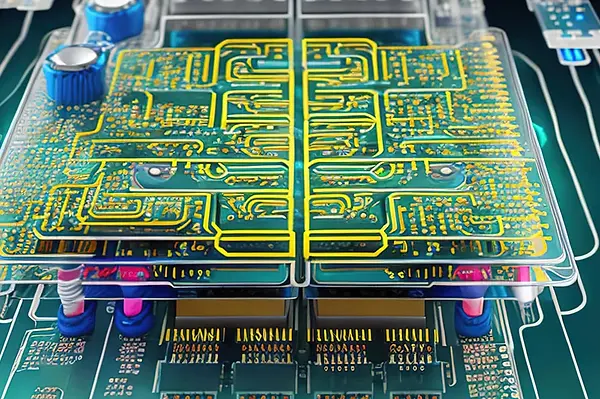
多層PCBの材料と構造
多層基板は、誘電体プリプレグとコア層によって分離された導電性銅層で構成されています。一般的な材料オプションをいくつか紹介します:
導電層:
ロール焼きなまし銅箔 (厚さ 1/2 ~ 3 オンス)
電気めっき銅箔
仕上げ: 銀、金、またはニッケルめっき
誘電体層:
FR-4 (ガラス強化エポキシ)
高 Tg エポキシ (高温安定性用)
RF/ワイヤレス ボード用 PTFE (テフロン)
ポリイミド (フレキシブル PCB 用)
シアネート エステル (レーダーおよび防衛アプリケーション用)
結合層:
FR-4 プリプレグ (部分的に硬化した樹脂)
Rogers プリプレグ
フッ素ポリマー接着フィルム
強化および非強化オプション
一般的な多層構造:
4 ~ 6 層: 低~中程度の複雑さ
8 ~ 10 層: より複雑なデジタル ボード
12 ~ 16 層: 高度な RF およびデータ処理
20 層以上: 極めて高密度な相互接続
60 層以上: 最先端の HDI テクノロジー
多層PCB設計の考慮事項
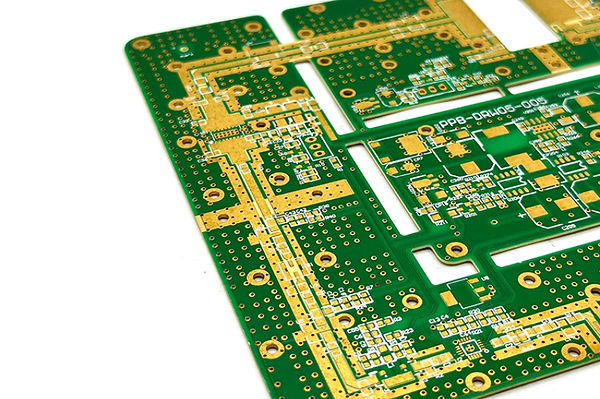
多層 PCB の設計には、相互接続密度、熱特性、製造上の制約、信号整合性の要因が高いため、課題があります。ここでは、主要な多層 PCB 設計ガイドラインを示します。
ボード スタックアップ:
電気的、熱的、CTE 特性に基づいて誘電体材料を選択します。
さまざまなラミネートの組み合わせでパフォーマンスをモデル化します。
可能な場合は対称構造を使用します。
各信号層にリファレンス プレーンを組み込みます。
プレーン層を慎重に割り当てます (グランド、電源、信号)。
高速ルーティング:
高速ネットにはインピーダンス制御ルーティングを使用します。
グランド/電源プレーン間に敏感なトレースを配置します。
差動ペアのトレース幅と間隔を一致させます。
急激な曲がり、スタブ、長さの不一致を最小限に抑えます。
適用環境でパフォーマンスをシミュレートします。
熱設計:
ホットスポットと熱拡散層をモデル化します。
熱伝導用のサーマル ビアを組み込みます。
熱拡散のために厚い銅プレーンを使用します。
熱伝導率のよい誘電体を選択します。
適切なコンポーネント間隔とエアフローを確保します。
シグナル インテグリティ:
レイヤー スタックアップを最適化してノイズ結合を分離します。
高速トレースのリターン パスを割り当てます。
一貫したリターンのためにメッキ スルー ホールを使用します。
コンデンサや抵抗器などの受動コンポーネントを組み込みます。
デカップリングと終端の規定を含めます。
電源分配:
電源の数に対して適切なピン配置を提供します。
アナログ回路とデジタル回路に別々のレギュレータ領域を使用します。
電源ソースの近くにバルク デカップリングを提供します。
分岐の長さを最小限に抑えるために電源プレーンを分配します。
コンポーネントのレイアウト:
高密度化のためにコンポーネントを両側に配置します。
コンポーネントをタイプ別にグループ化してルーティングを簡素化します。
コンポーネントがボード アウトライン内に収まるようにします。
必要に応じて再作業用のアクセス スペースを提供します。
ルーティング チャネル用のクリアランスを確保します。
レイヤー遷移:
可能な場合はレイヤーの変更を最小限に抑えます。
レイヤー遷移にはブラインド/埋め込みビアを使用します。
レイヤーを変更するときはトレース幅をテーパーにします。
インピーダンス遷移がスムーズになるようにします。
テスト可能性:
テスト ポイント、ポート、および電位プローブを含めます。
ベッド オブ ネイル テスト用のテスト パッドのグリッドを提供します。
可能な場合は組み込みのテスト構造を追加します。
デバッグ インターフェイス ポートへのアクセスを容易にします。
これらのガイドラインは、多層 PCB の信頼性、パフォーマンス、および製造可能性を確保し、現代の電子設計の複雑さに対処します。
モデリングと分析
材料特性、スタックアップ、コンポーネントレイアウト、配線密度間の複数の相互作用を考慮すると、効果的な多層 PCB 開発にはモデリング ツールが不可欠です。
電磁シミュレーション:
1. 放射、結合、共振をモデル化します。
2. スタックアップ、トレース形状、分割に関する問題を検出します。
3. 必要なシールドとグランド プレーンを特定します。
シグナル インテグリティ:
1. インピーダンスの不連続性と反射を分析します。
2. 終端戦略と伝送線路の影響を確認します。
3. 損失、ノイズ、結合を考慮します。
パワー インテグリティ:
1. DC および AC 電源特性をモデル化します。
2. 電力供給ネットワーク設計を確認します。
3. デカップリングと PDN の影響を含めます。
熱解析:
1. 負荷時の温度プロファイルを予測します。
2. コンポーネント レイアウトのホットスポットを特定します。
3. ヒートシンクと拡散の影響をモデル化します。
振動/衝撃解析:
1. 振動モードと共振を評価します。
2. 必要な機械的補強を特定します。
3. コンポーネントの取り付けとはんだ接合部の信頼性を確認します。
DFX 解析 (優れた設計):
1. 製造、組み立て、テストの設計を確認します。
2. 保守性と再作業の考慮事項を評価します。
3. 製造性、歩留まり、コストを改善します。
これらのモデリング ツールは、現代の電子設計に固有の複雑さに対処することで、多層 PCB の信頼性、パフォーマンス、製造性を保証します。
コストに関する考慮事項
多層 PCB の複雑さが増すと、製造コストが高くなります。主な要因は次のとおりです。
層数: 導電層が増えるごとに、イメージング、メッキ、ラミネーションのプロセス ステップが増えるため、コストが増加します。
ボード サイズ: ボードが大きいほど、容量の大きい機器が必要になり、通常は 24 インチ x 36 インチから 28 インチ x 44 インチの範囲になります。
高密度: トレースと間隔の許容範囲が狭くなり、穴のサイズが小さくなり、層が増えるため材料が薄くなるため、コストが増加します。複雑なパネル化とブレークアウトも費用を増加させます。
先端材料: 低損失ラミネート、薄いコア/プリプレグ、厚い銅、スタックされたマイクロビアなどの特殊な材料は高価です。
少量: 小規模な生産には非定期的なエンジニアリング料金が適用され、規模の経済を活用できません。
これらの要因を理解することは、多層 PCB 製造のコストを効果的に管理するために重要です。
コストに関する考慮事項
多層 PCB の信頼性に影響を与える主な要因は次のとおりです。
製造プロセス制御:
1. ドリルの位置決め精度が極めて優れている。
2. ボイドを防ぐための厳格なラミネート品質。
3. 連続性と接着性を確保するためのメッキの完全性。
ラミネート品質:
1. ガラス転移温度 (Tg) が高い。
2. 熱膨張係数 (CTE) が低い。
3. 吸湿特性が最小限である。
設計要因:
1. 内部層の効率的な放熱。
2. 十分な機械的補強と剛性。
3. 最適なコンポーネント レイアウトと密度。
テストと検査:
1. 自動光学検査 (AOI)。
2. 包括的なネット接続、回路内、および機能テスト。
3. 内部構造評価のための X 線分析。
4. メッキ品質を評価するための断面検査。
5. 温度、湿度、振動耐性に関する環境ストレステスト。
これらの要素は、多層 PCB の信頼性とパフォーマンスを確保するために重要です。
コストに関する考慮事項
多層 PCB 技術は、メッキされた穴とビアを介して相互接続された積層回路層を活用することで、より高密度で高性能な電子設計の作成を容易にします。これらの利点を実現するには、特殊な材料の選択と使用、高度なモデリング ツールの使用、洗練された熱および信号整合性技術の実装に関する熟練度が求められます。さらに、厳格なテストによる信頼性の確保と高度な製造プロセスの習得が不可欠です。この記事では、多層 PCB の機能について徹底的に概説し、現代の電子機器の厳しい要求を満たす堅牢な多層基板を効果的に設計、分析、製造するための知識をエンジニアに提供しました。