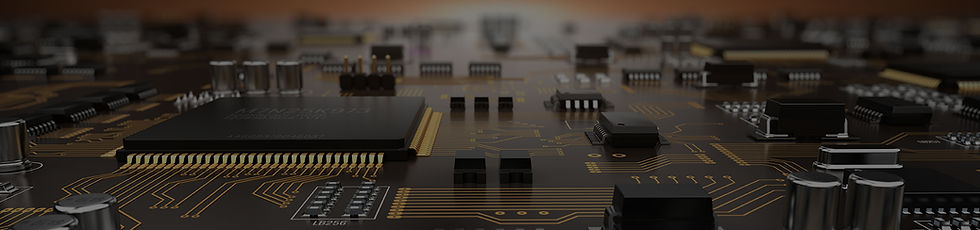
What Is A Box Build Assembly In PCB Electronics ?
SUNSOAR system integration services provide comprehensive Box Build assembly solutions, including Product Assembly, Cable Assembly, System-Level Assembly, and various testing capabilities for effective deployment. Currently, we cater to orders of fewer than 10,000 units.
Introduction
Box build assembly is the final stage of electronics manufacturing, encompassing the assembly of printed circuit boards (PCBs), cables, and various electronic components within a fully enclosed chassis or housing. This process blends mechanical, electrical, and aesthetic considerations to produce a finished electronic product ready for end-user deployment.
Executing box build assembly demands expertise in project management, meticulous supply chain coordination, stringent quality control practices, adept mechanical integration techniques, and comprehensive testing protocols. Companies specializing in box builds are typically referred to as contract manufacturers or electronic manufacturing services (EMS) providers.
What is Box Build Assembly
Overview of Box Build Assembly Process
Box build assembly encompasses several critical stages:
-
Kitting: Gathering all necessary materials including PCBs, cables, enclosures, fasteners, and accessories.
-
Sub-assembly: Integrating smaller modules such as power supplies, drives, and wire harnesses.
-
PCB Assembly: Mounting PCBs and electronic components into the enclosure using standoffs, screws, or adhesives. Interconnecting components with cables.
-
Integration: Adding supplementary elements like brackets, handles, and control interfaces to the enclosure.
-
Testing: Conducting rigorous quality assurance tests to ensure functionality, safety, and compliance with regulatory standards.
-
Packaging: Finalizing the product with user manuals, packaging, and labeling.
The complexity of box build assembly varies based on factors such as component diversity, enclosure intricacy, and production volume.
Benefits of Box Build Assembly
Utilizing box build assembly services offers several advantages:
-
Accelerated Time-to-Market: Expert contract manufacturers streamline product development and launch processes.
-
Focus on Core Competencies: Brands can concentrate on innovation and design while outsourcing manufacturing tasks.
-
Cost Efficiency: EMS providers leverage economies of scale in procurement and production, leading to cost savings.
-
Quality Assurance: Established EMS providers maintain stringent quality control measures and comprehensive testing protocols.
-
Flexibility and Scalability: Production volumes can be quickly adjusted to meet market demand fluctuations.
-
Comprehensive Service: EMS providers offer end-to-end solutions including sourcing, assembly, testing, logistics, and support services.

Industries Using Box Build Manufacturing
Some common industries that rely on box build assembly services:
-
Consumer electronics – Game consoles, home theaters, smart speakers
-
Industrial equipment – Power supplies, motor drives, automation controls, test instruments
-
Telecom/networking – Routers, switches, servers, base stations
-
Medical devices – Imaging systems, analyzers, monitors
-
Automotive – Navigation systems, EV charging stations, auto infotainment
-
Kiosks and vending – Self-checkout, ticketing kiosks, vending machines
-
Defense and aerospace – Ruggedized electronics, avionics boxes
Box Build Assembly Process Explained
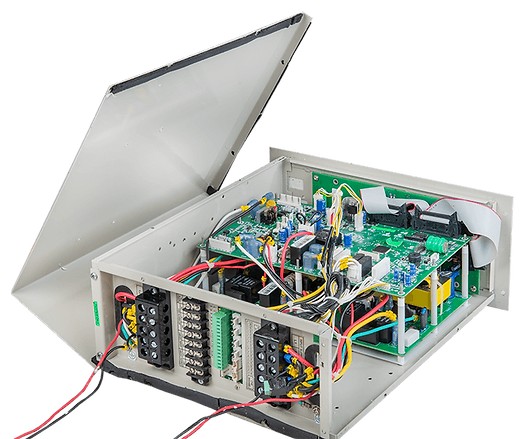
Kitting, also known as materials planning, initiates the box build assembly process by ensuring all necessary components and parts are procured in advance of production.
Components include:
-
Printed circuit boards (sourced from PCB suppliers or produced in-house via SMT lines)
-
Cables, wires, and connectors
-
Enclosures, brackets, and handles
-
Fasteners such as screws, rivets, and standoffs
-
Accessories like sensors, antennas, and keypads
-
Labels, packaging materials, and documentation
-
Assembly and testing tools
Efficient kitting prevents production delays due to missing parts and minimizes inventory holding costs. Components may be sourced globally from multiple suppliers, underscoring the importance of robust logistics and supply chain management.
Best Practices for Efficient Kitting:
-
Parts Classification: Categorize parts into groups (A, B, C) based on usage frequency, prioritizing high-demand Group A parts.
-
Min-Max Levels: Establish minimum and maximum inventory thresholds for each parts category to optimize stock levels.
-
Demand Planning: Utilize historical data and sales forecasts to anticipate future component requirements.
-
Lead Time Tracking: Consider lead times for components from various suppliers to prevent delays.
-
Visual Indicators: Implement Kanban systems and color coding to monitor parts consumption and replenishment needs.
-
Barcoding: Use barcoded labels for accurate parts identification and tracking throughout assembly processes.
-
Software Tools: Employ MRP (Material Requirements Planning) and ERP (Enterprise Resource Planning) systems for automated materials planning and inventory management.
Effective supply chain management is crucial for smooth box build assembly operations. Key practices include:
-
Vendor Selection: Evaluate suppliers based on qualifications and capabilities. Obtain compliance certificates and assess their ability to meet quality and delivery requirements.
-
Dual Sourcing: Mitigate risks associated with critical components by identifying and qualifying alternate suppliers.
-
Inventory Planning: Utilize demand forecasts and lead time analysis to optimize inventory levels. Implement strategies to balance stock availability with working capital requirements.
-
Purchase Orders: Ensure timely issuance of purchase orders to suppliers. Expedite orders as necessary to maintain production schedules.
-
Supplier Staging: Whenever feasible, localize suppliers near production facilities to streamline logistics and reduce lead times.
-
Logistics Optimization: Optimize shipment routes and modes of transportation to minimize costs and maximize efficiency. Consolidate shipments to achieve economies of scale.
A resilient supply chain strategy mitigates the risk of component shortages that could disrupt production schedules. Effective inventory management practices further enhance operational efficiency and financial stability.
Sub-Assembly
In complex box build assemblies, sub-assembly precedes final integration, streamlining the process by creating smaller, manageable modules. Common types of sub-assemblies include:
-
Power Supplies: AC-DC and DC-DC converters assembled separately due to component volume.
-
Drive Bays: Housing for hard drives and solid-state drives.
-
I/O Panels: Integration of ports, buttons, and display modules into accessible panels.
-
Wire Harnesses: Pre-assembled cables tailored to specific lengths and connector requirements.
Sub-assemblies enhance efficiency and quality by allowing independent testing to detect early defects. Reusable sub-assemblies from multiple production runs ensure consistency. Optimal granularity of sub-assemblies balances complexity and efficiency.
PCB Assembly
This phase involves mounting PCBs and electronic components onto metal or plastic enclosures. Considerations include:
-
Mounting: Utilizing pre-threaded holes, pillars, or standoffs for PCB attachment.
-
Thermal Design: Ensuring adequate heat dissipation and clearance within the enclosure.
-
Layout Planning: Facilitating assembly with sufficient component clearance and strategic connector placement.
Cabling and Wiring
Internal PCBs are interconnected using wires, cables, and connectors. Best practices include:
-
Routing: Employing wiring ducts, raceways, and strain reliefs for secure wire management.
-
Length Minimization: Shortening wire lengths to optimize routing and prevent overheating.
-
Labeling: Clearly marking cable ends to prevent miswiring, using unique connectors for identification.
Integration
Integrating additional components into the enclosure:
-
User Interface Elements: Buttons, switches, keypads, displays.
-
Mechanical Components: Brackets, handles, air vents, filters.
-
Branding: Logos, decals, regulatory markings.
Proper alignment and fit ensure functional and aesthetic coherence, reflecting industrial design and brand identity.
Testing and Quality Control
After mechanical assembly, rigorous testing ensures product reliability:
-
Functionality Testing: Verification of electrical safety, operational functionality, and environmental durability.
-
Safety and Compliance: Adherence to safety standards (UL, CE), electromagnetic compatibility (EMC/EMI), and environmental regulations (RoHS).

Product-Specific Tests
-
Visual Inspection: Ensures fit, finish, labeling accuracy, and overall cosmetic appearance.
-
Calibrations: Adjusts measurement electronics like signal generators for precise operation.
-
Burn-In Testing: Subjects products to prolonged powered operation to simulate environmental stresses.
-
Vibration, Drop, and Shock Testing: Conducted based on product application requirements.
-
Acoustic Testing: Measures sound levels and cooling fan noise to verify acoustic performance.
-
Thermal Testing: Monitors temperature distribution across enclosures using thermal probes.
Final Functional Audit
-
100% Functional Test: Ensures all units leaving production meet operational specifications.
-
Testing Criteria: Conforms to detailed product requirements and specifications.
-
Fault Detection and Correction: Identifies and resolves issues to ensure product reliability.
Comprehensive testing guarantees that each box build assembly meets stringent quality, safety, and reliability standards. Corrections are made proactively to deliver flawless products to customers.
Packaging and Logistics
The final steps include:
-
Attaching top and bottom covers or panels to fully enclose the chassis.
-
Applying protective plastic films over vulnerable areas.
-
Adding accessories like power cords, cables, brackets, CDs.
-
Inserting user manuals, warranty cards, registration leaflets.
-
Affixing labels with part numbers, serial numbers, logos, warnings, and certifications.
-
anti-static
-
Bubble wrap, foam, air cushions to protect the finished goods.
-
Packing each unit in an individual box with proper cushioning.
-
Palletizing boxes and shrink wrapping for shipment.
-
Coordinating logistics with customer’s warehouse or distribution centers.
Careful packaging prevents damage and improves the customer unboxing experience. The units are shipped via road, air, or sea as per lead time and geographic location.
Advantages of Using Box Build Assembly Services
Faster Time-to-Market
Outsourcing box builds to a contract manufacturer dramatically speeds up product launches and time-to-market.
Setting up an entire production line and facility in-house can take years and significant investment in tools and equipment. A specialized EMS provider, however, already has established assembly lines, supply chains, testing capabilities, and resources ready to go.
By entrusting detailed mechanical and electrical designs to the EMS provider, the product engineering team can accelerate the development cycle, bringing innovative products to market faster.
Key Accelerators of Time-to-Market:
-
Instant Production Readiness: Start production immediately using existing assembly lines.
-
Proven Efficiency: Leverage established manufacturing processes and quality systems.
-
Streamlined Supply Chain: Access a network of trusted suppliers for efficient part sourcing.
-
Flexible Scalability: Quickly adjust production volumes to meet demand fluctuations.
-
Rapid Prototyping: Iterate designs swiftly to optimize product features and performance.
Focus on Core Competencies
Brands and OEMs can concentrate internal resources on critical competencies such as product design, software development, and customer engagement. Delegating manufacturing operations allows for dedicated focus on innovation and market differentiation.
Contract manufacturers bring specialized skills, best practices, and rigorous quality standards to electronics manufacturing. This strategic outsourcing approach spares OEMs from hefty investments in production infrastructure and expertise development.
Areas for Enhanced Internal Focus:
-
Innovative Design: Pioneering product aesthetics and user experience.
-
Cutting-Edge Engineering: Advancing technological capabilities and intellectual property.
-
Software Differentiation: Crafting domain-specific software solutions and applications.
-
Brand Building: Elevating market presence and customer loyalty through strategic initiatives.
Cost Efficiency
Partnering with an established EMS provider leads to significant cost savings compared to in-house production.
-
Capital-Free Operation: Avoid upfront expenditures on equipment with flexible per-unit assembly costs.
-
Economies of Scale: Benefit from volume discounts on components through collective order aggregation.
-
Lean Inventory Management: Minimize stock levels with just-in-time (JIT) processes, reducing capital tied up in inventory.
-
Optimized Logistics: Lower shipping expenses with centralized logistics management.
Competitive Advantage
Reports suggest partnering with EMS providers can slash manufacturing costs by up to 30%, enhancing competitiveness and profitability.

Quality and Reliability
Electronics manufacturing requires consistency in soldering quality, part selection, testing methods, ESD control, and workmanship. Specialized EMS providers have institutional experience and expertise in quality control that is difficult to match with internal production.
Outsourcing box builds improves product reliability through:
-
Certified production facilities – ISO, IATF 16949, 5S workflows.
-
Automated processes – Error-proofing, inspection points, machine vision.
-
Latest tools – High precision equipment like selective soldering.
-
Skilled technicians – IPC certified soldering, assembly, and test engineers.
-
Components control – Approved vendor lists, counterfeit part prevention.
-
Repeatability – Standardized processes across products.
-
Reliability testing – HALT testing, burn-in, and environmental stress screening.
The end result is dependable products with lower warranty repair costs.
Flexibility and Scalability
EMS providers offer both low volume prototyping to high volume mass production. Customers can start with low rate initial production (LRIP) and rapidly scale up to demand. Sudden demand surges or shortages can be handled by rapidly adjusting capacity.
This flexibility comes from:
-
Modular assembly lines – Quickly add/remove equipment modules.
-
Multi-product lines – Schedule production across shared facilities.
-
Rapid changeovers – Switch between product variants efficiently.
-
Temporary workers – Meet peak demand using a flexible workforce.
-
JIT sourcing – Optimize and adjust orders with suppliers frequently.
The scalability and agility minimizes risks from demand fluctuations. New product introductions also benefit from the ramp up/ramp down capabilities.
One-Stop-Shop Services
The EMS partner provides a holistic set of services beyond just PCB assembly and boxing:
-
Product design – Design for manufacturability (DFM) inputs. PCB layout reviews. 3D modeling.
-
Prototyping – Functional prototyping of new product innovations.
-
Testing – Environmental stress testing. Compliance testing. Field failure analysis.
-
Supply chain – Sourcing components. Vendor managed inventory (VMI).
-
Sustaining engineering – Product maintenance. Obsolescence monitoring. Redesigns.
-
Repairs and warranty – Managing returns and repairs.
-
Distribution – Warehousing. Order fulfillment. Shipping.
Customers benefit from centralized cradle-to-grave support from industrial design to end-of-life management under one roof. The streamlined coordination also ensures better consistency across the product lifecycle.
Key Considerations for Box Build Project Success
Early Collaboration
Effective collaboration between the OEM and EMS partner at the outset is crucial for mitigating downstream issues. Focus on finalizing critical specifications early:
-
Industrial Design: Define enclosure materials, aesthetics, and branding.
-
Component Selection: Review Bill of Materials (BOM) for lead times, cost considerations, and potential obsolescence.
-
BOM Optimization: Identify substitute parts for cost-effectiveness and availability.
-
Design for Manufacturing (DFM): Conduct analysis to optimize for assembly and testing efficiency.
-
Manufacturing Processes: Establish quality plans and testing strategies.
-
Compliance Standards: Ensure alignment with safety, EMC/EMI, and regulatory requirements.
-
Project Schedule: Define timelines and production milestones.
Early collaboration and joint prototype builds preempt delays, ensuring requirements are met. Regular design reviews and progress checks maintain project momentum.
Quality Control Planning
Develop a robust quality plan encompassing:
-
Inspection Points: Implement in-process quality checks at critical stages.
-
Testing Methods: Include functional, environmental, reliability, and safety tests.
-
Traceability: Maintain part serialization, date codes, and comprehensive documentation.
-
ESD Protocols: Enforce electrostatic discharge control measures (e.g., wrist straps, mats).
-
Acceptance Criteria: Establish clear pass/fail metrics for inspections and tests.
-
Documentation: Utilize standardized forms and checklists for operational clarity.
-
Training: Provide rigorous training on test and inspection protocols.
-
Continuous Improvement: Conduct process capability analysis, set control limits, and implement corrective actions.
Rigorous attention to quality control from inception minimizes defects and ensures product reliability.
Manufacturing Process Development
Prepare assembly and testing processes for production readiness during prototyping:
-
Workflow Optimization: Streamline assembly steps for ergonomic efficiency.
-
Automation Feasibility: Evaluate options for automated processes such as screw driving.
-
Test Optimization: Debug and validate test routines for accuracy and reliability.
-
Process Validation: Conduct capability studies and establish control limits.
-
Operator Instructions: Develop visual work instructions and guides for clarity.
-
Training: Train personnel and regularly audit process adherence.
-
Fixture Design: Ensure assembly and test fixtures mirror final product configurations.
Comprehensive process development eliminates inefficiencies, paving the way for a seamless production ramp-up.
Supply Chain Management
Ensure proactive management of procurement and suppliers to optimize production efficiency:
-
Vendor Selection: Evaluate supplier qualifications, capabilities, and obtain compliance certificates.
-
Dual Sourcing: Mitigate risk by identifying alternative suppliers for critical components.
-
Inventory Planning: Strategically plan stocking levels based on demand forecasts and lead times.
-
Purchase Orders: Timely placement and expedited processing of part orders as necessary.
-
Supplier Staging: Optimize logistics by localizing suppliers near production facilities where feasible.
-
Logistics Optimization: Consolidate shipments and optimize routes for efficient part delivery.
A robust supply chain strategy prevents delays due to part shortages and minimizes working capital requirements through effective inventory management.