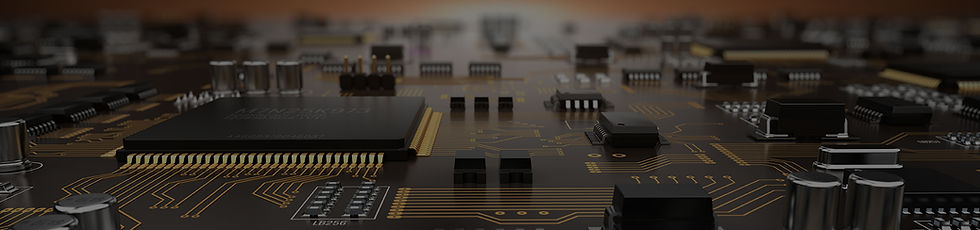
Introduction
High Density Interconnect (HDI) PCBs enable denser routing, finer lines and spaces, smaller vias, and increased layer counts compared to conventional PCBs. They are indispensable for compact and high-performance electronics such as smartphones, wearables, IoT devices, automotive electronics, and medical devices.
Choosing the right HDI PCB manufacturer is critical to achieving high yields, superior quality, and on-time delivery for both prototyping and large-scale production. This article presents a comprehensive guide listing the top 18 global HDI PCB manufacturers, along with a structured framework for evaluating their capabilities and selecting the ideal partner.
-
Rigid Flex PCB

Overview of HDI PCBs
High Density Interconnect (HDI) refers to a PCB technology that utilizes microvias, smaller than traditional vias, to achieve denser interconnections between layers.
Key features include:
-
Trace/space widths ≤ 100 μm (3.9 mils)
-
Microvias ≤ 150 μm with a diameter to hole ratio of ≥ 20:1
-
Thin dielectric layers ≤ 60 μm
-
Capability for more than 10 layers
-
Finer pad geometries and tighter pitch components like 0201, 01005 discretes, and BGAs
Benefits of HDI technology include:
-
Miniaturization of PCBs, enabling more compact designs
-
Enhanced signal integrity with tight impedance control
-
Facilitation of high-density routing through specialized routing channels
-
Support for complex designs with over 30 layers
-
Increased component densities and isolation of analog and digital signals
HDI PCBs necessitate specialized manufacturing processes and equipment not commonly found in standard PCB manufacturing facilities. Choosing a manufacturer with dedicated HDI capabilities is essential for achieving optimal performance and reliability in high-density electronic applications.

HDI PCB Manufacturers
Key Considerations for Selecting an HDI Partner:
Technical Capabilities:
-
Fine line width/spacing: Preferably 2 μm or lower
-
Microvia size: Typically in the range of 50 μm to 80 μm
-
Number of HDI build-up layers: Ideal to have more than 20 layers
-
Handling of thin cores: Typically 25 μm to 35 μm
-
Laser drilling diameters: Below 50 μm
-
Blind and buried vias: Essential for dense interconnects
-
Stacked or staggered microvias: Depending on design requirements
Quality & Reliability:
-
Certification: IPC 6012 Class 3 and Class 3A for HDI standards
-
Quality processes: Includes AOI, comprehensive testing, inspection, and statistical process control
-
Reliability testing: IST, HAST, drop/shock/vibration tests
Volume Production:
-
Monthly capacity: Number of panels per month
-
On-time delivery: Consistent metrics
-
Experience: Years in mass production of HDI boards
Customer Service:
-
Technical expertise: Offering layout reviews and DFM feedback
-
Responsiveness: Quotation, sample, and inquiry turnaround times
-
Supply chain transparency: Reporting and visibility
-
Customer feedback: Reviews and testimonials
Cost:
-
HDI pricing: Varied by complexity and layer count
-
NRE charges: Prototyping costs
-
Budgetary estimates: Provided before finalizing designs
Location:
-
Proximity: Production sites near key customers
-
Global presence: Ensures production redundancy and support
Carefully evaluating potential manufacturers against these criteria facilitates the selection of an ideal HDI partner suited to specific project needs.

HDI PCB technology enables miniaturized electronics design through high density interconnects, fine features, and thin materials. As products become thinner and lighter, HDI provides the means to pack more functionality and components into tight spaces. Partnering with specialized manufacturers that have invested in advanced HDI capabilities and processes is crucial to realize the benefits of next-gen PCB technologies. This article provided an overview of the top 18 HDI PCB manufacturers globally and a framework to match specific product needs with the right manufacturing partner. The key is early supplier engagement to understand capabilities and limitations before finalizing designs. Investing upfront in DFM and manufacturability will ensure high yields and repeatable quality when transitioning to volume HDI production.