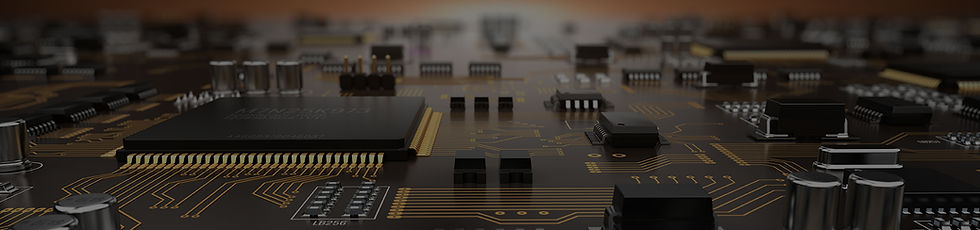
Introduction
Flexible printed circuit boards (PCBs), also known as flex circuits, provide advanced capabilities beyond conventional rigid PCBs. Their flexible construction allows for bending, folding, and dynamic flexing, making them essential for modern electronics.
Overview of Flexible PCB Technology:
Materials and Construction:
-
Substrates: Polyimide or polyester for excellent thermal and electrical properties.
-
Conductive Layers: Rolled annealed or electro-deposited copper.
-
Adhesives and Coverlays: Acrylic or epoxy-based adhesives for protection and stability.
Key Properties:
-
Flexibility: Ability to bend and twist without damage.
-
Durability: Resistance to vibrations and mechanical stress.
-
Lightweight: Reduces device weight.
Design Considerations:
-
Bend Radius: Avoid stress fractures.
-
Trace Routing: Careful routing to minimize stress.
-
Layer Stackup: Optimize for mechanical properties and signal integrity.
Types and Applications:
-
Single-Sided: Simple applications.
-
Double-Sided: More complex designs.
-
Multilayer: High-density interconnections.
-
Rigid-Flex: Combines flexible and rigid sections.
Advantages:
-
Space-saving, lightweight, high flexibility, fewer connectors.
Limitations:
-
Higher initial costs, complex manufacturing, potential for mechanical damage.
Flex vs. Rigid PCBs:
-
Flexibility: Flex PCBs bend; rigid PCBs do not.
-
Durability: Flex for dynamic; rigid for static applications.
-
Cost: Flex PCBs have higher costs but can reduce overall system costs.
Future Trends:
-
Wearable Technology: Increasing demand.
-
Advanced Materials: Improved performance.
-
Miniaturization: Smaller, more complex devices.
Understanding flexible PCB technology helps effectively utilize flex circuits in electronic products, enhancing performance and enabling innovative applications.
-
Dupont Material
-
2 Layer FPC
-
Multilayer Fpc

What is a Flex PCB?
A flex PCB, or flexible printed circuit board, utilizes a dielectric base layer made of flexible polymer materials such as polyimide or polyester. Conductive copper traces are laminated onto this flexible base layer, creating a thin, bendable circuit board. Unlike rigid PCBs that use fiberglass reinforcement, flex PCBs can be dynamically flexed and contorted during use, providing unique advantages for modern electronic applications.
Common Names for Flex PCBs:
-
Flex circuits
-
Flexible circuits
-
Flexible printed circuits
-
Flex prints
Key Properties of Flex PCBs:
-
Flexible: Capable of bending, twisting, and folding to conform around structures.
-
Lightweight: Made from extremely thin flexible material, reducing overall device weight.
-
Dynamic: Can endure repeated flexing, rolling, and folding without damage.
-
Durable: Designed to withstand millions of flex cycles, ensuring long-term reliability.
-
Integrated: Interconnects can serve as components themselves, simplifying design.
-
Space-Saving: Allows tight integration with compact products, optimizing space utilization.
-
Customizable: Can be fabricated in any 2D shape to meet specific design requirements.
Applications and Benefits: Flex PCBs are particularly well-suited for compact, portable electronic devices where traditional rigid boards cannot meet the physical and electrical demands. They are commonly used in applications such as smartphones, wearable technology, medical devices, and aerospace electronics due to their flexibility, durability, and ability to fit into complex and constrained spaces. By leveraging the unique properties of flex PCBs, designers can create more innovative and efficient electronic products.

Flexible PCB Materials and Construction
Flexible printed circuit boards (PCBs) are designed with unique materials and construction techniques that enable their distinct capabilities. The key components of a flex circuit’s build are:
Dielectric Flexible Substrate: The base dielectric layer forms the foundation for the conductive traces. Choosing the appropriate flexible substrate material is crucial. Common options include:
-
Polyimide (Kapton): Most popular choice, high-temperature rating, excellent chemical resistance.
-
Polyester (PET): Lower cost, moderately high-temperature rating.
-
Polyamide: Remains flexible even at low temperatures.
-
Fluoropolymers (PTFE): Superior chemical resistance, relatively expensive.
-
Liquid Crystal Polymer (LCP): High frequency, low signal loss.
Polyimide is the most widely used substrate material due to its high durability, thermal properties, and cost-benefit ratio.
Copper Foil: An ultrathin rolled annealed copper foil is laminated onto the base substrate. Typical foil thicknesses in flex PCBs range from 12μm to 35μm (0.5 oz to 1 oz). The thinnest option is selected based on current-carrying needs to maximize flexibility.
Conductors: The copper foil is patterned using lithographic processes to create the required conductive paths or traces. A subtractive process is typically employed for flex PCB conductor fabrication.
Coverlay: A thin flexible dielectric coverlay is laminated over the conductor layer for insulation and protection. Coverlay thickness is usually 25 to 50μm. Common materials for coverlay include Kapton or polyester films.
Bonding Adhesive: Acrylic or epoxy-based adhesive films bond the base substrate with the copper foil and the coverlay with the conductors. These adhesives ensure effective adhesion while maintaining flexibility.
Stiffeners: Additional dielectric stiffening layers may be incorporated in multilayer constructions to minimize wrinkling or buckling of the flex PCB due to thermal stresses.
Finish and Coatings: A solder mask coats the conductor pattern for insulation and oxidation prevention. Surface finishes like Hot Air Solder Leveling (HASL) can be applied to exposed pads for additional protection.
By utilizing these specialized materials and construction techniques, flexible PCBs achieve the necessary properties to meet the complex physical and electrical demands of modern electronic devices.

Key Properties of Flexible PCBs
Flexible PCBs possess unique properties derived from their materials and construction methods, making them suitable for various advanced applications:
Thickness: Overall thickness ranges from 12 μm for simple single-layer constructions to around 180 μm for complex multilayer boards, enabling extremely thin and lightweight circuits.
Bend Radius: Flex PCBs can be bent to tight radii down to 3 times the thickness. Dynamic flexing down to 10 times the thickness is achievable for some constructions.
Heat Resistance: Polyimide bases provide heat resistance up to 400°C, allowing flex PCBs to withstand reflow soldering temperatures. Other materials offer lower maximum temperatures.
Chemical Resistance: The substrates offer good chemical resistance to common fluxes and solvents used during assembly and soldering processes.
Weight: The lightweight polyimide or polyester substrates make flex PCBs 80-90% lighter than equivalent rigid laminates.
High Frequency Performance: Short signal paths and thin dielectrics provide excellent high-frequency performance. Substrates like Liquid Crystal Polymer (LCP) offer superior RF properties.
Current Ratings: Copper thickness limits current carrying capacity, with typical continuous current ratings ranging from approximately 0.5A to 5A for common flex circuit constructions.
By carefully selecting suitable materials and adhering to design rules, the properties of flexible PCBs can be optimized to meet specific application requirements, ensuring reliable performance in various electronic devices.
Flexible PCB Design Considerations
Designing a reliable flexible PCB requires addressing the dynamic bending aspects with specialized guidelines:
Trace Width and Spacing: Wider spacing for narrower traces in dynamic regions is essential to avoid cracks. A 2:1 ratio of spacing to trace width is recommended.
Bend Radius: Route traces perpendicular to bend axes. Maintain at least a 3X base thickness for static bends and 10X for dynamic bends.
Coverlay Voids: Minimize voids where traces are exposed to prevent wear, especially in dynamic bend zones.
Reinforcement: Use stiffeners in multilayer regions to prevent buckling and wrinkling during bending.
Adhesives: Employ high-performance flexible adhesives like acrylic for durability in dynamic flex applications.
Vias: Use tear-drop shaped vias with adequate annular rings to prevent crack propagation from drill hole edges.
Corners: Round sharp trace corners with higher radii to reduce stress concentrations. Avoid angled traces at corners.
Pads: Utilize rounded rectangle or circular pads and thermally relieve pads in flexing areas with neckdowns.
By following these guidelines, flex PCBs can be designed to withstand millions of flexing cycles, ensuring long product lifetimes and reliability in various applications.
Common Flex PCB Types and Applications
Flex PCBs are versatile in various configurations for interconnect and packaging applications:
Flexible Interconnects: Utilize conductor traces to connect PCBs, displays, and modules over hinges or slides, accommodating dynamic movements.
Flexible Cables: Parallel conductor traces on rolled flex substrates create high-density ribbon cables for signals, data, and power interconnections.
Membrane Switches: Integrate conductor traces, spacers, and flexible overlays for ultra-thin touch-sensitive control switches.
Flex Rigid Boards: Combine rigid sections with flexible areas, enabling compact folding while retaining complex rigid structures.
Flexible Heaters: Nickel-chromium alloy traces on flex substrates form thin, conformable heating pads and blankets for versatile heating applications.
Applications:
-
Medical instruments
-
Wearable devices
-
Robotics and industrial machines
-
Consumer electronics
-
Automotive electronics
-
Aerospace and military systems
Flex PCBs, with their compactness, lightweight nature, and dynamic capabilities, enable innovative designs across various industries.
Benefits and Advantages of Flex PCBs
Here are some of the key benefits provided by flexible PCB technology:
Dynamic Flexing – Withstand millions of movement cycles enabling rolling, twisting, folding which is impossible with rigid PCBs.
Conforms to Shape – Can tightly integrate with product contours and housings unlike rigid boards.
Lightweight – Extremely low mass compared to rigid laminates allows portable, wearable devices.
Thin Form Factor – Compact, low-profile circuits to fit small spaces and enable thinner products.
Durable – Flexible construction is resistant to vibrations and mechanical shocks.
High Density – Integrates interconnects avoiding external cables and connectors.
Custom Shapes – Can be produced in unlimited 2D shapes and outlines.
Soft and pliable – Allows integration of complete electronic systems into fabrics.
Reliability – Offers consistent performance over flex life with proper design.
Cost Savings – Removes connectors, simplifies assembly and lowers total product cost.
Limitations and Challenges
While offering many advantages, flexible PCB technology also poses the following limitations:
Limited layers and density – Typical 1-6 layers allows only simpler circuits. High density multilayer flex is still developing.
Lower current ratings – Copper thickness limits current carrying capacity typically under 5A.
Challenging assembly – Requires specialized SMT processes suitable for flexible substrates.
Prone to wear – Improper dynamic flex spacing causes cracks and conductor failures.
Requires backing structure – Flex circuits need assembly onto rigid frames or enclosures for full system integration.
Thermal management concerns – The insulating polymer substrate hinders heat dissipation.
Susceptible to environmental damage – Hence additional protective encapsulation is necessary.
With sound design practices and progress in materials, these limitations are constantly being addressed to expand flex PCB capabilities.
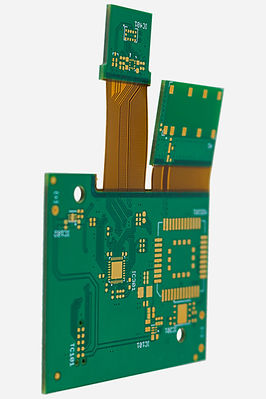
Future Trends in Flexible PCBs
Looking ahead, the evolution of flexible PCB technology is poised to advance with several key trends:
-
Thinner Constructions: Pushing the limits with flexible layer thicknesses as low as 1 mil, enhancing bendability without compromising performance.
-
Smaller Features: Narrower trace widths and spacing down to 2 mils, enabling higher integration density in compact electronic devices.
-
Improved Materials: Introducing advanced substrates like Liquid Crystal Polymer (LCP) for superior electrical and high-frequency performance, meeting the demands of next-generation applications.
-
Fine Pitch Components: Facilitating the direct surface mount of ultra-fine pitch ICs on flexible PCBs, supporting miniaturization and functionality in small form factor devices.
-
High Density Flex: Developing flexible multilayer boards with up to 12 conductive layers, offering enhanced functionality and complexity in electronic designs.
-
Embedding Passives: Integrating thin embedded resistors and capacitors within flexible layers, optimizing space and improving signal integrity.
-
Stretchable Circuits: Exploring novel materials to enable flexible PCBs that can stretch and deform, opening new possibilities in wearable electronics and biomedical applications.
-
Additive Processing: Advancing from traditional subtractive etching to additive fabrication methods such as printing or plating, enhancing precision and efficiency in manufacturing.
-
3D Structured Flex Circuits: Innovating techniques to fabricate out-of-plane flex circuit structures, enabling more complex and customized electronic assemblies.
As these trends converge with advancements in material science and manufacturing capabilities, flexible PCB technology will catalyze innovation, enabling unprecedented designs and functionalities across diverse industries.
Conclusion and Summary
-
Flex PCB technology leverages specialized materials and construction for flexible, lightweight, and dynamic circuits.
-
Polyimide stands out as the predominant flexible dielectric substrate, paired with ultrathin copper foils for conductivity.
-
Flex PCBs support tight bend radii, ranging from 3 to 10 times the total thickness, facilitating versatile design applications.
-
Design considerations are crucial to ensure optimal dynamic flex performance and reliability.
-
Flex circuits are prevalent in compact and portable electronic devices that require flexibility and durability.
-
While offering unique advantages, flex PCBs have limitations in terms of layer count, density, and power handling capabilities.
-
Ongoing advancements aim to achieve thinner profiles, higher density, and enhanced performance.
-
With their unique capabilities and advantages, flexible PCBs will continue to expand as a pivotal interconnection solution, driving electronics miniaturization across diverse industries.