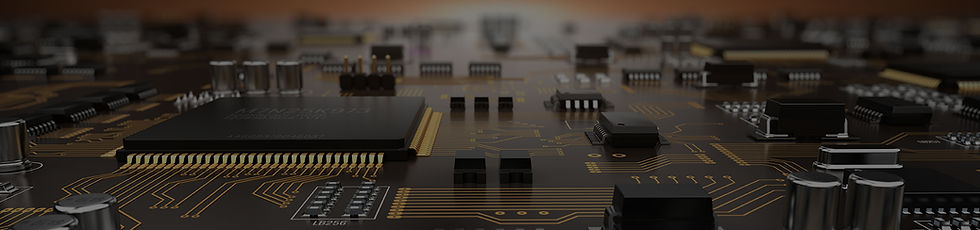
¿Qué es un conjunto de construcción de caja en electrónica PCB?
Los servicios de integración de sistemas de SUNSOAR brindan soluciones integrales de ensamblaje de cajas, que incluyen ensamblaje de productos, ensamblaje de cables, ensamblaje a nivel de sistema y diversas capacidades de prueba para una implementación eficaz. Actualmente, atendemos pedidos de menos de 10 000 unidades.
Introducción
El ensamblaje de cajas es la etapa final de la fabricación de productos electrónicos, que abarca el ensamblaje de placas de circuito impreso (PCB), cables y diversos componentes electrónicos dentro de un chasis o carcasa completamente cerrado. Este proceso combina consideraciones mecánicas, eléctricas y estéticas para producir un producto electrónico terminado listo para su implementación por parte del usuario final.
La ejecución del ensamblaje de cajas exige experiencia en gestión de proyectos, coordinación meticulosa de la cadena de suministro, prácticas estrictas de control de calidad, técnicas de integración mecánica expertas y protocolos de prueba exhaustivos. Las empresas que se especializan en ensamblajes de cajas suelen denominarse fabricantes por contrato o proveedores de servicios de fabricación electrónica (EMS).
-
Ensamblaje de caja
-
Ensamblaje de prototipo
-
PCB multicapa
-
Prueba de PCBA
¿Qué es el ensamblaje de cajas?
Descripción general del proceso de ensamblaje de la caja
El ensamblaje de la caja comprende varias etapas críticas:
1. Preparación: Recolección de todos los materiales necesarios, incluidos PCB, cables, carcasas, sujetadores y accesorios.
2. Subensamblaje: Integración de módulos más pequeños, como fuentes de alimentación, unidades y mazos de cables.
3. Ensamblaje de PCB: Montaje de PCB y componentes electrónicos en la carcasa mediante separadores, tornillos o adhesivos. Interconexión de componentes con cables.
4. Integración: Adición de elementos complementarios, como soportes, manijas e interfaces de control, a la carcasa.
5. Pruebas: Realización de rigurosas pruebas de control de calidad para garantizar la funcionalidad, la seguridad y el cumplimiento de las normas reglamentarias.
6. Empaquetado: Finalización del producto con manuales de usuario, empaquetado y etiquetado.
La complejidad del ensamblaje de la caja varía según factores como la diversidad de componentes, la complejidad de la carcasa y el volumen de producción.
Beneficios del ensamblaje de cajas
El uso de servicios de ensamblaje de cajas ofrece varias ventajas:
1. Tiempo de comercialización más rápido: los fabricantes por contrato expertos agilizan los procesos de desarrollo y lanzamiento de productos.
2. Enfoque en las competencias básicas: las marcas pueden concentrarse en la innovación y el diseño mientras subcontratan las tareas de fabricación.
3. Rentabilidad: los proveedores de EMS aprovechan las economías de escala en la adquisición y la producción, lo que genera ahorros de costos.
4. Garantía de calidad: los proveedores de EMS establecidos mantienen estrictas medidas de control de calidad y protocolos de prueba integrales.
5. Flexibilidad y escalabilidad: los volúmenes de producción se pueden ajustar rápidamente para satisfacer las fluctuaciones de la demanda del mercado.
6. Servicio integral: los proveedores de EMS ofrecen soluciones integrales que incluyen abastecimiento, ensamblaje, pruebas, logística y servicios de soporte.

Branchen, die Box-Build-Fertigung nutzen
Einige gängige Branchen, die auf Box-Build-Montagedienste angewiesen sind:
Unterhaltungselektronik – Spielkonsolen, Heimkinos, intelligente Lautsprecher
Industrieausrüstung – Stromversorgungen, Motorantriebe, Automatisierungssteuerungen, Testinstrumente
Telekommunikation/Netzwerk – Router, Switches, Server, Basisstationen
Medizinische Geräte – Bildgebungssysteme, Analysatoren, Monitore
Automobil – Navigationssysteme, Ladestationen für Elektrofahrzeuge, Auto-Infotainment
Kioske und Verkaufsautomaten – Selbstbedienungskassen, Ticketkioske, Verkaufsautomaten
Verteidigung und Luft- und Raumfahrt – Robuste Elektronik, Avionikboxen
Explicación del proceso de ensamblaje de la caja
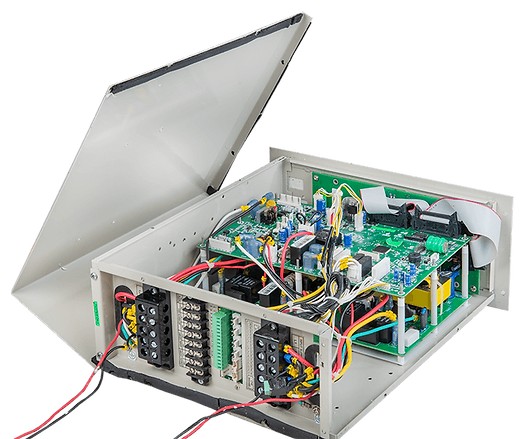
La preparación de kits, también conocida como planificación de materiales, inicia el proceso de ensamblaje de la caja al garantizar que todos los componentes y piezas necesarios se adquieran antes de la producción.
Los componentes incluyen:
1. Placas de circuitos impresos (obtenidas de proveedores de PCB o producidas internamente a través de líneas SMT)
2. Cables, alambres y conectores
3. Cajas, soportes y manijas
4. Sujetadores como tornillos, remaches y separadores
5. Accesorios como sensores, antenas y teclados
6. Etiquetas, materiales de embalaje y documentación
7. Herramientas de ensamblaje y prueba
La preparación de kits eficiente evita demoras en la producción debido a piezas faltantes y minimiza los costos de mantenimiento de inventario. Los componentes pueden obtenerse globalmente de múltiples proveedores, lo que subraya la importancia de una logística sólida y una gestión de la cadena de suministro.
Mejores prácticas para la preparación eficiente de kits:
Clasificación de piezas: clasifique las piezas en grupos (A, B, C) según la frecuencia de uso, priorizando las piezas del grupo A de alta demanda.
Niveles mínimos y máximos: establezca umbrales de inventario mínimos y máximos para cada categoría de piezas para optimizar los niveles de existencias.
Planificación de la demanda: utilice datos históricos y pronósticos de ventas para anticipar los requisitos futuros de componentes.
Seguimiento del tiempo de entrega: considere los tiempos de entrega de los componentes de varios proveedores para evitar demoras.
Indicadores visuales: implemente sistemas Kanban y códigos de colores para monitorear el consumo de piezas y las necesidades de reposición.
Códigos de barras: use etiquetas con códigos de barras para la identificación y el seguimiento precisos de las piezas durante los procesos de ensamblaje.
Herramientas de software: emplee sistemas MRP (planificación de requisitos de materiales) y ERP (planificación de recursos empresariales) para la planificación automatizada de materiales y la gestión de inventario.
Una gestión eficaz de la cadena de suministro es crucial para que las operaciones de montaje de cajas se lleven a cabo sin problemas. Las prácticas clave incluyen:
Selección de proveedores: evaluar a los proveedores en función de sus calificaciones y capacidades. Obtener certificados de cumplimiento y evaluar su capacidad para cumplir con los requisitos de calidad y entrega.
Doble abastecimiento: mitigar los riesgos asociados con los componentes críticos mediante la identificación y calificación de proveedores alternativos.
Planificación de inventario: utilizar pronósticos de demanda y análisis de plazos de entrega para optimizar los niveles de inventario. Implementar estrategias para equilibrar la disponibilidad de existencias con los requisitos de capital de trabajo.
Órdenes de compra: garantizar la emisión oportuna de las órdenes de compra a los proveedores. Agilizar los pedidos según sea necesario para mantener los cronogramas de producción.
Preparación de proveedores: siempre que sea posible, localizar a los proveedores cerca de las instalaciones de producción para agilizar la logística y reducir los plazos de entrega.
Optimización de la logística: optimizar las rutas de envío y los modos de transporte para minimizar los costos y maximizar la eficiencia. Consolidar los envíos para lograr economías de escala.
Una estrategia de cadena de suministro resiliente mitiga el riesgo de escasez de componentes que podría interrumpir los cronogramas de producción. Las prácticas eficaces de gestión de inventario mejoran aún más la eficiencia operativa y la estabilidad financiera.
Subconjunto
En conjuntos complejos de construcción en caja, el subconjunto precede a la integración final, lo que agiliza el proceso mediante la creación de módulos más pequeños y manejables.
Los tipos comunes de subconjuntos incluyen:
Fuentes de alimentación: convertidores CA-CC y CC-CC ensamblados por separado debido al volumen de los componentes.
Bahías de unidad: carcasas para discos duros y unidades de estado sólido.
Paneles de E/S: integración de puertos, botones y módulos de pantalla en paneles accesibles.
Mazos de cables: cables preensamblados adaptados a longitudes específicas y requisitos de conector.
Los subconjuntos mejoran la eficiencia y la calidad al permitir pruebas independientes para detectar defectos tempranos. Los subconjuntos reutilizables de múltiples tiradas de producción garantizan la consistencia. La granularidad óptima de los subconjuntos equilibra la complejidad y la eficiencia.
Ensamblaje de PCB
Esta fase implica el montaje de PCB y componentes electrónicos en carcasas de metal o plástico. Las consideraciones incluyen:
Montaje: uso de orificios pre-roscados, pilares o separadores para la fijación de PCB.
Diseño térmico: garantizar la disipación de calor y el espacio libre adecuados dentro del gabinete.
Planificación del diseño: facilitar el ensamblaje con suficiente espacio libre para los componentes y la ubicación estratégica de los conectores.
Cableado y cableado
Las PCB internas se interconectan mediante cables y conectores. Las mejores prácticas incluyen:
Enrutamiento: utilizar conductos para cableado, canales y protectores contra tirones para una gestión segura de los cables.
Minimización de la longitud: acortar la longitud de los cables para optimizar el enrutamiento y evitar el sobrecalentamiento.
Etiquetado: marcar claramente los extremos de los cables para evitar un cableado incorrecto, utilizando conectores únicos para su identificación.
Integración
Integración de componentes adicionales en el gabinete:
Elementos de la interfaz de usuario: botones, interruptores, teclados, pantallas.
Componentes mecánicos: soportes, manijas, respiraderos, filtros.
Marca: logotipos, calcomanías, marcas reglamentarias.
La alineación y el ajuste adecuados garantizan la coherencia funcional y estética, lo que refleja el diseño industrial y la identidad de la marca.
Pruebas y control de calidad
Tras el montaje mecánico, se realizan pruebas rigurosas para garantizar la fiabilidad del producto:
Pruebas de funcionalidad: verificación de la seguridad eléctrica, la funcionalidad operativa y la durabilidad ambiental.
Seguridad y cumplimiento: cumplimiento de las normas de seguridad (UL, CE), compatibilidad electromagnética (EMC/EMI) y normativas ambientales (RoHS).

Pruebas específicas del producto
1. Inspección visual: garantiza el ajuste, el acabado, la precisión del etiquetado y la apariencia cosmética general.
2. Calibraciones: ajusta los componentes electrónicos de medición, como los generadores de señales, para lograr un funcionamiento preciso.
3. Pruebas de quemado: somete los productos a un funcionamiento prolongado con energía para simular tensiones ambientales.
4. Pruebas de vibración, caídas e impactos: se realizan según los requisitos de aplicación del producto.
5. Pruebas acústicas: mide los niveles de sonido y el ruido del ventilador de enfriamiento para verificar el rendimiento acústico.
6. Pruebas térmicas: monitorea la distribución de la temperatura en los gabinetes mediante sondas térmicas.
Auditoría funcional final
1. Prueba funcional del 100 %: garantiza que todas las unidades que salen de producción cumplan con las especificaciones operativas.
2. Criterios de prueba: cumple con los requisitos y especificaciones detallados del producto.
3. Detección y corrección de fallas: identifica y resuelve problemas para garantizar la confiabilidad del producto.
Las pruebas exhaustivas garantizan que cada conjunto de cajas cumple con estrictos estándares de calidad, seguridad y confiabilidad. Se realizan correcciones de manera proactiva para entregar productos impecables a los clientes.
Embalaje y logística
Los pasos finales incluyen:
1. Colocar las cubiertas o paneles superiores e inferiores para encerrar completamente el chasis.
2. Aplicar películas plásticas protectoras sobre las áreas vulnerables.
3. Agregar accesorios como cables de alimentación, cables, soportes, CD.
4. Insertar manuales de usuario, tarjetas de garantía, folletos de registro.
5. Colocar etiquetas con números de pieza, números de serie, logotipos, advertencias y certificaciones.
antiestático
1. Envoltura de burbujas, espuma, cojines de aire para proteger los productos terminados.
2. Empacar cada unidad en una caja individual con la amortiguación adecuada.
3. Paletizar las cajas y envolverlas en plástico retráctil para el envío.
4. Coordinar la logística con el almacén o los centros de distribución del cliente.
Un embalaje cuidadoso evita daños y mejora la experiencia del cliente al abrir la caja. Las unidades se envían por carretera, aire o mar según el tiempo de entrega y la ubicación geográfica.
Ventajas de utilizar los servicios de ensamblaje de Box Build
Tiempo de comercialización más rápido
La subcontratación de la fabricación de cajas a un fabricante por contrato acelera drásticamente los lanzamientos de productos y el tiempo de comercialización.
Establecer una línea de producción completa y una instalación interna puede llevar años y una inversión significativa en herramientas y equipos. Sin embargo, un proveedor de EMS especializado ya cuenta con líneas de montaje, cadenas de suministro, capacidades de prueba y recursos listos para funcionar.
Al confiar diseños mecánicos y eléctricos detallados al proveedor de EMS, el equipo de ingeniería de productos puede acelerar el ciclo de desarrollo y llevar productos innovadores al mercado más rápido.
Aceleradores clave del tiempo de comercialización:
Disponibilidad de producción instantánea: comience la producción de inmediato utilizando líneas de montaje existentes.
Eficiencia comprobada: aproveche los procesos de fabricación y los sistemas de calidad establecidos.
Cadena de suministro optimizada: acceda a una red de proveedores confiables para obtener piezas de manera eficiente.
Escalabilidad flexible: ajuste rápidamente los volúmenes de producción para satisfacer las fluctuaciones de la demanda.
Prototipos rápidos: repita los diseños rápidamente para optimizar las características y el rendimiento del producto.
Centrarse en las competencias básicas
Las marcas y los fabricantes de equipos originales pueden concentrar los recursos internos en competencias críticas como el diseño de productos, el desarrollo de software y la interacción con el cliente. Delegar las operaciones de fabricación permite centrarse exclusivamente en la innovación y la diferenciación en el mercado.
Los fabricantes por contrato aportan habilidades especializadas, mejores prácticas y rigurosos estándares de calidad a la fabricación de productos electrónicos. Este enfoque de subcontratación estratégica evita a los fabricantes de equipos originales grandes inversiones en infraestructura de producción y desarrollo de conocimientos.
Áreas para un mayor enfoque interno:
Diseño innovador: ser pioneros en la estética de los productos y la experiencia del usuario.
Ingeniería de vanguardia: avanzar en las capacidades tecnológicas y la propiedad intelectual.
Diferenciación de software: crear soluciones y aplicaciones de software específicas para cada dominio.
Construcción de marca: aumentar la presencia en el mercado y la lealtad del cliente a través de iniciativas estratégicas.
Relación coste-eficiencia
Asociarse con un proveedor de EMS establecido genera importantes ahorros de costes en comparación con la producción interna.
Operación sin capital: evitar gastos iniciales en equipos con costes de montaje por unidad flexibles.
Economías de escala: Benefíciese de descuentos por volumen en componentes mediante la agregación de pedidos colectivos.
Gestión de inventarios eficiente: Minimice los niveles de existencias con procesos justo a tiempo (JIT), lo que reduce el capital inmovilizado en el inventario.
Logística optimizada: Reduzca los gastos de envío con una gestión logística centralizada.
Ventaja competitiva
Los informes sugieren que asociarse con proveedores de EMS puede reducir los costos de fabricación hasta en un 30 %, lo que mejora la competitividad y la rentabilidad.

Calidad y confiabilidad
La fabricación de productos electrónicos requiere consistencia en la calidad de la soldadura, la selección de piezas, los métodos de prueba, el control de ESD y la mano de obra. Los proveedores de EMS especializados tienen experiencia institucional y conocimientos en control de calidad que son difíciles de igualar con la producción interna.
La subcontratación de la fabricación de cajas mejora la confiabilidad del producto a través de:
1. Instalaciones de producción certificadas: ISO, IATF 16949, flujos de trabajo 5S.
2. Procesos automatizados: detección de errores, puntos de inspección, visión artificial.
3. Herramientas de última generación: equipos de alta precisión como soldadura selectiva.
4. Técnicos calificados: ingenieros de soldadura, ensamblaje y prueba certificados por IPC.
5. Control de componentes: listas de proveedores aprobados, prevención de piezas falsificadas.
6. Repetibilidad: procesos estandarizados en todos los productos.
7. Pruebas de confiabilidad: pruebas HALT, pruebas de quemado y detección de estrés ambiental.
El resultado final son productos confiables con menores costos de reparación bajo garantía.
Flexibilidad y escalabilidad
Los proveedores de EMS ofrecen desde prototipos de bajo volumen hasta producción en masa de alto volumen. Los clientes pueden comenzar con una producción inicial de bajo ritmo (LRIP) y escalar rápidamente según la demanda. Los aumentos repentinos de demanda o la escasez se pueden manejar ajustando rápidamente la capacidad.
Esta flexibilidad proviene de:
1. Líneas de ensamblaje modulares: agregue o elimine rápidamente módulos de equipos.
2. Líneas de múltiples productos: programe la producción en instalaciones compartidas.
3. Cambios rápidos: cambie entre variantes de productos de manera eficiente.
4. Trabajadores temporales: satisfaga la demanda máxima utilizando una fuerza laboral flexible.
5. Abastecimiento JIT: optimice y ajuste los pedidos con los proveedores con frecuencia.
La escalabilidad y la agilidad minimizan los riesgos de las fluctuaciones de la demanda. Las introducciones de nuevos productos también se benefician de las capacidades de aumento o disminución gradual.
Servicios integrales
El socio de EMS ofrece un conjunto integral de servicios que van más allá del ensamblaje y el empaquetado de PCB:
1. Diseño de productos: insumos de diseño para la fabricación (DFM). Revisiones de diseños de PCB. Modelado 3D.
2. Creación de prototipos: creación de prototipos funcionales de innovaciones de nuevos productos.
3. Pruebas: pruebas de estrés ambiental. Pruebas de cumplimiento. Análisis de fallas en campo.
4. Cadena de suministro: obtención de componentes. Inventario administrado por el proveedor (VMI).
5. Ingeniería de mantenimiento: mantenimiento de productos. Monitoreo de obsolescencia. Rediseños.
6. Reparaciones y garantía: gestión de devoluciones y reparaciones.
7. Distribución: almacenamiento. Cumplimiento de pedidos. Envío.
Los clientes se benefician de un soporte centralizado de principio a fin, desde el diseño industrial hasta la gestión del fin de la vida útil, todo en un solo lugar. La coordinación optimizada también garantiza una mejor consistencia en todo el ciclo de vida del producto.
Wichtige Überlegungen für den Erfolg von Box Build-Projekten
Colaboración temprana
La colaboración eficaz entre el OEM y el socio de EMS desde el principio es crucial para mitigar los problemas posteriores. Concéntrese en finalizar las especificaciones críticas de manera temprana:
Diseño industrial: defina los materiales, la estética y la marca de la carcasa.
Selección de componentes: revise la lista de materiales (BOM) para conocer los plazos de entrega, las consideraciones de costos y la posible obsolescencia.
Optimización de la lista de materiales: identifique las piezas sustitutivas para lograr una mejor relación costo-beneficio y disponibilidad.
Diseño para la fabricación (DFM): realice análisis para optimizar la eficiencia del ensamblaje y las pruebas.
Procesos de fabricación: establezca planes de calidad y estrategias de prueba.
Estándares de cumplimiento: garantice la alineación con los requisitos de seguridad, EMC/EMI y reglamentarios.
Programa del proyecto: defina los plazos y los hitos de producción.
La colaboración temprana y las construcciones conjuntas de prototipos evitan los retrasos, lo que garantiza que se cumplan los requisitos. Las revisiones de diseño y los controles de progreso regulares mantienen el impulso del proyecto.
Planificación del control de calidad
Desarrolle un plan de calidad sólido que abarque:
Puntos de inspección: implemente controles de calidad en proceso en etapas críticas.
Métodos de prueba: incluya pruebas funcionales, ambientales, de confiabilidad y de seguridad.
Trazabilidad: mantenga la serialización de las piezas, los códigos de fecha y la documentación completa.
Protocolos ESD: aplique medidas de control de descarga electrostática (por ejemplo, muñequeras, tapetes).
Criterios de aceptación: establezca métricas claras de aprobación/desaprobación para las inspecciones y pruebas.
Documentación: utilice formularios y listas de verificación estandarizados para lograr claridad operativa.
Capacitación: proporcione capacitación rigurosa sobre protocolos de prueba e inspección.
Mejora continua: realice análisis de capacidad del proceso, establezca límites de control e implemente acciones correctivas.
La atención rigurosa al control de calidad desde el inicio minimiza los defectos y garantiza la confiabilidad del producto.
Desarrollo del proceso de fabricación
Prepare los procesos de ensamblaje y prueba para la preparación de la producción durante la creación de prototipos:
Optimización del flujo de trabajo: agilice los pasos de ensamblaje para lograr una eficiencia ergonómica.
Viabilidad de la automatización: evalúe las opciones para procesos automatizados como el atornillado.
Optimización de pruebas: depure y valide las rutinas de prueba para lograr precisión y confiabilidad.
Validación del proceso: realice estudios de capacidad y establezca límites de control.
Instrucciones para el operador: Desarrolle instrucciones y guías de trabajo visuales para mayor claridad.
Capacitación: Capacite al personal y audite regularmente el cumplimiento del proceso.
Diseño de accesorios: Asegúrese de que los accesorios de ensamblaje y prueba reflejen las configuraciones del producto final.
El desarrollo integral del proceso elimina las ineficiencias, allanando el camino para una aceleración de la producción sin inconvenientes.
Gestión de la cadena de suministro
Asegure una gestión proactiva de las adquisiciones y los proveedores para optimizar la eficiencia de la producción:
Selección de proveedores: Evalúe las calificaciones y capacidades de los proveedores y obtenga certificados de cumplimiento.
Abastecimiento dual: Mitigue el riesgo identificando proveedores alternativos para componentes críticos.
Planificación de inventario: Planifique estratégicamente los niveles de existencias según los pronósticos de demanda y los plazos de entrega.
Órdenes de compra: Colocación oportuna y procesamiento acelerado de pedidos de piezas según sea necesario.
Preparación de proveedores: Optimice la logística ubicando a los proveedores cerca de las instalaciones de producción cuando sea posible.
Optimización de la logística: Consolide los envíos y optimice las rutas para una entrega eficiente de piezas.
Una estrategia sólida de la cadena de suministro evita demoras debido a la escasez de piezas y minimiza los requisitos de capital de trabajo mediante una gestión eficaz del inventario.